First note: the Advanced Materials Industrial Consortium annual meeting is just around the corner! Friday, September 11 we will be meeting in the Engineering Centers Building on campus. If you haven't registered yet, please do so for our planning purposes. REGISTER HERE. We have been carefully considering feedback and ideas from past events and are trying out a different format with focused parallel technical sessions led by faculty moderators in four areas: Microstructured thin films and coatings, Advanced Materials Characterization, Electronics Materials and Devices, and Bio-materials and Biotechnology. The faculty will give a general overview of the areas and spotlight talks in specific areas which can be given by students, postdocs or industrial partners. In addition, we have structured networking opportunities to enhance interactions between attendees which include speed networking and an ice cream social. We hope to see you at the meeting!
AMIC sponsored a booth at the Wisconsin Science and Technology Symposium at UW River Falls in late July. It was great to see the Wisys crew and to be exposed to the lively research and networking activity there! Below are a few pictures (Photo credit, Susann Ely, Wisconsin Materials Institute):
|
WSTS 2015 participants in discussion including Elizabeth Glogowski (UW Eau Claire) and Seth King (UW La Crosse) |
|
Bob Wise (Wisys) and Ozgur Yavuzcetin (UW Whitewater, Physics)
|
|
Jon McCarthy (RM2N) and Tony Wagner (UW Eau Claire) |
We also attended the Office of Corporate Relations (OCR) open house in mid August. It was useful to learn more about how the OCR is able to give a broad set of options to companies seeking to engage with UW Madison. One set of features mentioned was the professional development courses offered through various departments and schools. More information can be found here: https://advanceyourcareer.wisc.edu . We congratulate our colleagues at the OCR on a very well attended and successful event!
The Regional Materials and Manufacturing Network (RM2N) kick-off meeting in September 21-22 is being held at UW Eau Claire.
You may have heard about the Regional Industrial Network and the Regional Materials and Manufacturing Network (RM2N) - if not, come join us to learn more about how this new network will help coalesce resources and capabilities in the region by engaging startups, small and large manufacturers, and harnessing the network and cutting edge research and instrumentation within the University of Wisconsin system!
As always, if you have questions, suggestions or comments, please let us know!
Best regards,
Felix Lu and Erin Gill,
Co-Directors, UW AMIC
|
Engagement with UW-Madison
|
|
Industry Sponsored Research Roadmap |
The flowchart shows some of the possible pathways sponsored research between UW Madison and a company may take. The Office of Corporate Relations (OCR) partners with industry to facilitate broad engagements with UW-Madison that reach across schools and colleges. OCR also mediates negotiations with the Office of Industrial Partnerships (OIP) and the Wisconsin Alumni Research Foundation (WARF) regarding sponsored research. AMIC partners with its members to enable a range of engagements from facilities use or fee-for-service to sponsored capstone projects to sponsored research. Depending on the existence of background intellectual property (IP), either with the company or with the university, and the potential for new IP, a sponsored research agreement is negotiated with OIP that may include IP terms negotiated with WARF that enable downstream commercialization. Representatives from OCR, OIP and WARF will be in attendance at the AMIC annual meeting if you have additional questions.
|
|
At Midwest Prototyping, an employee removes devices that hold six GoPro cameras from the nylon powder they were created from. (Bill Fritsch) |
Leave it to some UW engineering students to figure out a way to improve upon 3-D desktop printers and gain national recognition for their efforts.
Cédric Kovacs-Johnson, Chase Haider, and Taylor Fahey were out to build a 3-D desktop printer that printed in color, so shortly after graduating, the group formed Spectrom.
"In 2009, a few people saw an opportunity to build a cheaper FDM 3-D industrial printer for between $1,000 and $2,000," Kovacs-Johnson explains. "The first few models were rudimentary, but they kind of built a new industry in a new model."
As the technology evolved, the students saw 3-D printing technology becoming more streamlined and reliable, and desktop printers more plentiful. Instead of having one $100,000 printer in an engineering office, for example, smaller desktop printers were appearing on individual engineer's desks. But the ability to print in color remained a challenge
That was the problem the young men set out to solve.
"Right now, people wanting their 3-D desktop to print in color have to set several hot nozzles, usually with messy results and mechanical complexities. It's a bad model," Kovacs-Johnson says.
The need for color is a no-brainer. "Think about it," he challenges. "How often do people request black and white photos anymore? We've come to expect color, and once people see 3-D objects coming out in color, there's no looking back."
Spectrom's customizable software brings reliable, on-demand color to 3-D desktop printers, much like an inkjet printer. The company also manufactures its own consumables - proprietary plastics and dyes - creating an automated system for color.
"Our opportunity was not to build a printer and compete with everyone, but to work with everyone to integrate our product inside their printers, like Intel," Kovacs-Johnson says.
Colors will be true, he promises. The software will be given away for free while the add-on hardware will be a component designed to work with compatible 3-D printers. Revenue will be generated by hardware sales and consumables.
The company is in the final stages of R&D and making software improvements. "The end goal is not just to be an add-on component, but to be integrated in all 3-D printers being sold out there," Kovacs-Johnson notes.
The group's biggest obstacle - reducing transition time between colors - is where Kovacs-Johnson says Spectrom really broke new ground. "We spent nine months researching just that aspect. That's what our patents are around."
That's also what evidently swayed the judges. In November, the company took top honors at the Collegiate Inventors Competition in Virginia, despite strong competition from a field of 112 teams representing colleges including Harvard, Johns Hopkins, Columbia, Clemson, and UNC-Chapel Hill.
Read more:
http://www.ibmadison.com/In-Business-Madison/August-2015/3-D-vision/index.php?cparticle=1&siarticle=0#artanc
|
|
Employees from different sectors work side by side to get products in and out of the laboratory at record speed at Dental Crafters. Photo courtesy of Dental Crafters. |
More choices. Better. More customized. Faster.
That's what today's consumer wants.
And in the wake of the recession and the evolution of the digital age, customers also are willing (and able) to shop around for the perfect fit.
The result is a proliferation of customized products in the global marketplace over the past few years. From staircases that come in thousands of designs and soda bottles that come in hundreds of shapes and sizes to dozens of highly specialized machines including oil drills, conveyor belts, and dental restoration products, today's products are being designed to meet the diverse needs and fancies of the global and connected consumer.
This has come as a benefit to some. A recent Strategy& report found that in the United States, small manufacturers (with revenues of less than $1 billion) grew at twice the compound annual rate of large manufacturers (with revenues of more than $3 billion) between 2009 and 2012.
But not to all. Larger companies are struggling to position themselves to be competitive in this more and more specialized and
|
Ananth Krishnamurthy, Associate Professor |
competitive marketplace. How can they satisfy the consumer's desire for high quality and customization while still producing products rapidly at a mass scale?
This is one of the questions that led top CEOs, CFOs, COOs, and management professionals from around the world to come to Madison in late-June 2015 for the 14th International Conference on
"Quick response manufacturing (QRM) provides an enterprise-wide management strategy that can produce high-quality customized products at record speed and with fewer losses," says Ananth Krishnamurthy, an associate professor of industrial and systems engineering and the QRM Center's director.
Read more:
http://www.engr.wisc.edu/news/archive/2015/July8a.html
|
|
UW-Madison and Oshkosh Corporation officials pose in front of an airport firefighting vehicle manufactured by the company. Chancellor Rebecca Blank visited to strengthen ties between Oshkosh Corporation and the university. Photos courtesy of Oshkosh Corporation
|
Sometimes seeing what University of Wisconsin-Madison alumni are working on demands a truck ride over gravel moguls, through fields of rubble and up hills pitched like church steeples.
After seeing firsthand the technologies that Oshkosh Corporation is building in Wisconsin and sending around the world, UW-Madison Chancellor Rebecca Blank stressed the value of collaboration between premier public research institutions and companies such as Oshkosh, which employs nearly 100 UW-Madison alumni.
"These collaborations drive innovation and I will do everything I can to strengthen these ties and bring more research to market," Blank said during a July 22 visit to the company's headquarters.
Not only do many UW-Madison graduates find careers at Oshkosh Corporation, but the College of Engineering has worked closely with the company on a range of projects as varied as Formula One racing to restoring "The Bucky Wagon," a 1932 fire truck featured in the annual homecoming parade, which now has a body from Pierce Manufacturing, an Oshkosh Corporation brand.
The vehicle that took Blank and three engineering professors smoothly over the moguls during their visit could be a game changer for the company. The Department of Defense (DoD) is considering the vehicle, named the Light Combat Tactical All-Terrain Vehicle (L-ATV), for the military's next-generation light protected vehicle program, dubbed the Joint Light Tactical Vehicle (JLTV) program.
Read more:
http://news.wisc.edu/23913?utm_source=iUW&utm_medium=email&utm_campaign=iUW2015-08-04
|
The Advanced Materials Industrial Consortium (AMIC) annual meeting is being held
on Friday, Sept. 11, 2015 at the Tong Auditorium in the Engineering Centers Building at the UW Madison campus.
Join us for the annual meeting of the UW-AMIC. You don't have to be a
member of the consortium to attend. All are welcome. The agenda includes multiple industry speakers, parallel focused topic sessions, networking opportunities, an instrument talk and facilities tours.
If you need hotel reservations, please contact Ms. Jennifer Weber ([email protected], (608) 265-3783.
Agenda
2015 AMIC Meeting
Friday, September 11
7:30 Breakfast
8:20 Keynote (Dr. Shou Wong, DOW)
8:50 Industry Talk (Mr. Kevin Nelson, BEMIS)
9:20 BREAK
9:35 PARALLEL TECHNICAL SESSION I
Biomaterials & Biotechnology (Prof. David Lynn)
Electronic Materials & Devices (Prof. Tom Kuech)
10:50 BREAK
11:00 Materials Informatics Brainstorming (Prof. Dane Morgan)
11:20 Industry Talk (Dr. Bryce Nelson, Sigma-Aldrich)
11:50 Speed Networking
12:15 LUNCH (& posters)
1:45 PARALLEL TECHNICAL SESSION II
Microstructured Thin FIlms & Coatings (Prof. Padma Gopalan)
Adv. Materials Characterization (Prof. Paul Voyles)
3:00 BREAK (With Babcock Ice Cream)
3:15 Industry Talk (Dr. Eric Nordberg, Brady Corp.)
4:00 Facilities Tours
5:00 Adjourn meeting
|
|
Water Treatment Project Engineer, Chen Li, autoclaving liquids at the A. O. Smith water treatment lab located at the Global Water Center in Milwaukee, Wisconsin.
|
A.O. Smith
"Innovation Has a Name" not only summarizes A. O. Smith's vision, it helps describe the rich 141-year history of this diversified, global manufacturer. The Milwaukee-based company is one of the world's leading manufacturers and marketers of residential and commercial water heaters, boilers, and water purification products with more than 12,400 employees at plants in the U.S., Mexico, Canada, China, India, Turkey, and the Netherlands. The publicly traded company (AOS-NYSE) reported 2014 sales of $2.36 billion.
A. O. Smith is North America's largest manufacturer of residential and commercial water heaters for many of the best-known brands in the water heater industry, including A. O. Smith, State, American, GSW (Canada) and John Woods (Canada). Its comprehensive commercial product line includes gas and electric standard water heaters and gas, electric and oil-fired specialty (custom) commercial products. The company also manufactures a line of high-efficiency, copper-tube boilers and large-volume hot water tanks. Its extensive line of residential gas and electric water heaters range in size from 2 to 120 gallons and include a number of high-efficiency products. To support its product development efforts worldwide, Water Products Company has engineering centers in the U.S., Canada, China, and the Netherlands.
A. O. Smith is one of largest and best-known residential water heater brands in China and the only U. S. water heater company with a significant presence in that country. A. O. Smith markets an extensive line of gas, electric, solar, and tankless water heaters specifically designed for Chinese consumers as well as gas and electric commercial water heating equipment. The company first entered the Chinese market in 1996 and has grown its volume and market share substantially since then.
|
Senior Technician, David Morris, taking electrical measurements of the control system of a commercial water heater at the A. O. Smith Corporate Technology Center in Milwaukee, Wisconsin.
|
In 2009, the company entered the rapidly growing market for water purification products and has grown to become one of the leading brands in China. The company also manufactures point of use reverse osmosis water treatment products under the A. O. Smith brand and several private brands, and serves the residential and light commercial market segments in China.
A. O. Smith was the first U. S. company to enter the Indian residential water heater market when it opened a water heater manufacturing plant in Bangalore in 2010 and later launched a line of water treatment products for the Indian market in 2015.
Interested in a career in engineering or technology?
For career opportunities, including internships and co-ops, visit
www.aosmith.com
|
UW Materials Science in the news
|
|
Diagram of oxygen reduction reaction using an icosahedral (20-faced) nanoparticle structure catalyst of palladium and platinum. Image courtesy of Manos Mavrikakis, professor of chemical and biological engineering at the University of Wisconsin-Madison. |
Every engineer knows the importance of platinum catalysts in various industries, including manufacturing, automotive, chemical and more. An unfortunate drawback of the catalysts is that they are often rare and expensive.
However, researchers have discovered that using icosahedral (20-faced) nanoparticle structures for palladium/platinum catalysts reduces the cost and increases catalytic activity.
Currently, palladium is used as a cheaper alternative to platinum for catalytic functions such as car muffler systems.
What sets this new catalyst apart, however, is this new atomic arrangement. Additionally, the amount of platinum used in the palladium/platinum catalysts surface is kept to a minimum. None the less, researchers found that smaller amounts of the new catalyst were able to improve the catalytic activity in comparison to platinum and palladium alone.
"This is speaking to the precise arrangement of atoms on the surface of a nanoparticle," says Manos Mavrikakis, professor of chemical and biological engineering at the University of Wisconsin-Madison (UW-Madison). "That can make an enormous difference in how fast the reaction takes place. Theory has been instrumental for about 10 years now to demonstrate the importance of being able to tailor-make specific facets of the same material."
He added, "The goal here is to try to minimize the amount of platinum that you use, and eventually find a complete replacement of platinum. If we can move away from platinum, many of these applications have the potential to become more robust financially."
The current catalytic set-up used to test the palladium/platinum material is an oxygen reduction reaction typically seen in fuel cells. However, the research offers chemical engineers suggestions on how to design custom catalysts, on the atomic scale, for various applications using nanoparticles and quantum mechanics.
Read more:
http://www.engineering.com/Education/EducationArticles/ArticleID/10382/Atomic-Arrangement-of-Catalysts-Boosts-Efficiency-and-Reduces-Cost.aspx
|
Throughout the University of Wisconsin System, there is a wealth of materials expertise, equipment and research facilities - but connecting those resources across campuses and between academia and industry often depends on serendipity and informally built connections.
"There are so many collaborations that come about because you met someone at a conference and they're doing something related to what you're doing or have capabilities you're looking for," says Gokul Gopal, an assistant professor of engineering physics at UW-Platteville. "It tends to happen through almost random encounters rather than a systematic portal that allows you to access information in a smoother manner."
Partners across the system are filling that void through the recently established Regional Materials and Manufacturing Network (RM2N). The network is currently developing features on its website to allow academic and industrial partners from all over Wisconsin to list and search for the resources they have and need, to advance materials science and engineering through both academic research and the development of new products. The initial member campuses in the network are UW-Eau Claire, UW-La Crosse, UW-Madison, UW-Milwaukee, UW-Platteville, UW-Stevens Point and UW-Stout.
The network will help all the institutions involved expand their efforts and make the most of what's already here in the state. "I think part of it is, to do what we do in materials science is expensive," says Doug Dunham, director of the Materials Science Center at UW-Eau Claire. "Instrumentation in particular is very expensive. It doesn't make sense in many cases for multiple copies of one type of instrument to be located at seven different campuses in Wisconsin. Instead, let's make it so someone has it but everyone has access to it."
Read more:
http://news.wisc.edu/23886
|
In the quest for better, less expensive ways to store and use energy, platinum and other precious metals play an important role. They serve as catalysts to propel the most efficient fuel cells, but they are costly and rare.
Now, a metal-free alternative catalyst for fuel cells may be at hand. In a study published July 15 in ACS Central Science, a team of chemists from the University of Wisconsin-Madison introduces a new approach that uses a molecular catalyst system instead of solid catalysts. Although molecular catalysts have been explored before, earlier examples were much less efficient than the traditional platinum catalyst.
A fuel cell converts chemical energy into electricity by reacting hydrogen and oxygen at two different electrodes. A catalyst makes the reaction more efficient.
UW-Madison chemistry Professor Shannon Stahl and lab scientist James Gerken took inspiration from their group's previous work with catalysts that use oxygen in applications for the chemical industry. They noticed a striking similarity between these aerobic oxidation reactions and the oxygen reaction in fuel cells and decided to see if they could apply a similar approach to a fuel cell.
The new catalyst is composed of a mixture of molecules called nitroxyls and nitrogen oxides. These molecular partners play well together; one reacts well with the electrode while the other reacts efficiently with the oxygen.
"While this catalyst combination has been used previously in aerobic oxidations, we didn't know if it would be a good fuel cell catalyst," Stahl says. "It turns out that it is the most effective molecular catalyst system ever reported."
Read more:
http://news.wisc.edu/23894?
|
|
A diagram shows an optical nanoresonator embedded within a slab of low-index material to test its performance. |
University of Wisconsin-Madison engineers have created a nanoscale device that can emit light as powerfully as an object 10,000 times its size. It's an advance that could have huge implications for a variety of imaging and energy applications.
In a paper published July 10, 2015 in the journal Physical Review Letters,
Zongfu Yu, an assistant professor of electrical and computer engineering at UW-Madison, and his collaborators describe nanoscale device that that drastically outpaces previous technology in its ability to scatter light. They showed how a single nanoresonator can manipulate light to cast a very large "reflection." The nanoresonator's capacity to absorb and emit light energy is such that it can make itself-and, in applications, other very small things-appear 10,000 times as large as its physical size.
"Making an object look much 10,000 times larger than its physical size has lots of implications in technologies related to light," Yu says.
The researchers realized the advance through materials innovation and a keen understanding of the physics of light. Much like sound, light can resonate, amplifying itself as the surrounding environment manipulates the physical properties of its wave energy. The researchers took advantage of this by creating an artificial material in which the wavelength of light is much larger than in a vacuum, which allows light waves to resonate more powerfully.
The device condenses light to a size smaller than its wavelength-meaning it can gather a lot of light energy-and then scatters the light over a very large area-meaning its output can be harnessed for imaging applications that make microscopic particles appear huge.
"The device makes an object super-visible by enlarging its optical appearance with this super-strong scattering effect," Zhou says.
Read more:
http://phys.org/news/2015-07-nanoscale-device-emit-powerfully-size.html
|
|
A transmission electron microscope image shows a typical sample of platinum cubic nanocages. (Credit: Xia Laboratory) |
Posted July 23, 2015 | Atlanta, GA
A new fabrication technique that produces platinum hollow nanocages with ultra-thin walls could dramatically reduce the amount of the costly metal needed to provide catalytic activity in such applications as fuel cells.
The technique uses a solution-based method for producing atomic-scale layers of platinum to create hollow, porous structures that can generate catalytic activity both inside and outside the nanocages. The layers are grown on palladium nanocrystal templates, and then the palladium is etched away to leave behind nanocages approximately 20 nm in diameter, with between three and six atom-thin layers of platinum.
Use of these nanocage structures in fuel cell electrodes could increase the utilization efficiency of the platinum by a factor of as much as seven, potentially changing the economic viability of the fuel cells.
"We can get the catalytic activity we need by using only a small fraction of the platinum that had been required before," said Younan Xia, a professor in the Wallace H. Coulter Dept. of Biomedical Engineering at Georgia Tech and Emory Univ. Xia also holds joint faculty appointments in the School of Chemistry and Biochemistry and the School of Chemical and Biomolecular Engineering at Georgia Tech. "We have made hollow nanocages of platinum with walls as thin as a few atomic layers because we don't want to waste any material in the bulk that does not contribute to the catalytic activity."
The research-which also involved researchers at the Univ. of Wisconsin-Madison, Oak Ridge National Laboratory, Arizona State Univ. and Xiamen Univ. in China-was reported in Science.
Platinum is in high demand as a catalyst for a wide range of industrial and consumer applications. The high cost of platinum needed for the catalysts deposited on electrodes has limited the ability to use low-temperature fuel cells in automobiles and home applications.
In catalytic applications, only the surface layers of platinum contribute to the chemical reaction, leading researchers to develop new structures designed to maximize the amount of platinum exposed to reactants. The hollowing out process reduces the amount of the precious metal not contributing to the reaction, and allows the use of larger nanocrystals that are less susceptible to sintering, an aggregation phenomenon which reduces catalyst surface area.
Read more:
http://www.news.gatech.edu/2015/07/23/ultra-thin-hollow-nanocages-could-reduce-platinum-use-fuel-cell-electrodes?
|
|
HemoLink, an inexpensive, disposable, needleless blood collection device, may be available to consumers by 2016. It uses a process called "capillary action" to draw blood into a collection tube. Users simply place it on their arm or stomach for two minutes, and then mail the tube to a medical laboratory for analysis. (Photos copyright Tasso, Inc.) Read more: New Microfluidic Blood-draw Device Could Replace Needle Sticks and Venipunctures at Medical Laboratories | Dark Daily http://www.darkdaily.com/new-microfluidic-blood-draw-device-could-replace-needle-sticks-and-venipunctures-at-medical-laboratories-817#ixzz3jOQp4n00 |
By placing this low-cost, disposable device developed at the University of Wisconsin-Madison on their arms or abdomens, patients can collect their own blood at home in minutes
For more than two years, the nation's media have been captivated by
Theranos CEO
Elizabeth Holmes' vision of offering patients who need blood tests a finger stick collection instead of a
venipuncture. Meanwhile, in research labs across the nation, there are credible efforts to develop ways to collect
medical laboratory test specimens that require no needles at all.
On such effort may soon enter the market. It is an innovative, needleless blood-collection device called
HemoLink developed by a research team at the University of Wisconsin-Madison. Users simply place a device with the diameter of a golf ball against their arms or abdomens for two minutes. During that time, the device draws blood from capillaries into a small container. Patients would then mail the tube of collected blood to a
medical laboratory for analysis.
This non-threatening device is ideal for children. However, patients who require recurrent blood tests to monitor health conditions would also benefit, as it would save them frequent trips to clinical laboratories for blood draws using traditional needle-stick methods.
How the HemoLink Device Works
In a process known as "
capillary action," HemoLink leverages
microfluidics to create a slight vacuum that pulls blood from capillaries though tiny channels in the skin into a small tube, noted a
Gizmag report. The device collects 0.15 cubic centimeters of blood, which is enough to test for cholesterol, infections, cancer cells, blood sugar and other conditions.
Read more:
http://www.darkdaily.com/new-microfluidic-blood-draw-device-could-replace-needle-sticks-and-venipunctures-at-medical-laboratories-817#axzz3jMQ3rF8r
|
Researchers at the Univ. of Maryland (UMD) recently discovered that paper made of cellulose fibers is tougher and stronger the smaller the fibers get. For a long time, engineers have sought a material that is both strong (resistant to non-recoverable deformation) and tough (tolerant of damage).
"Strength and toughness are often exclusive to each other," said Teng Li, associate professor of mechanical engineering at UMD. "For example, a stronger material tends to be brittle, like cast iron or diamond."
The UMD team pursued the development of a strong and tough material by exploring the mechanical properties of cellulose, the most abundant renewable bio-resource on Earth. Researchers made papers with several sizes of cellulose fibers-all too small for the eye to see-ranging in size from about 30 um to 10 nm. The paper made of 10-nm-thick fibers was 40 times tougher and 130 times stronger than regular notebook paper, which is made of cellulose fibers a thousand times larger.
"These findings could lead to a new class of high performance engineering materials that are both strong and tough, a Holy Grail in materials design," said Li.
High-performance yet lightweight cellulose-based materials might one day replace conventional structural materials (metals) in applications where weight is important. This could lead, for example, to more energy-efficient and "green" vehicles. In addition, team members say, transparent cellulose nanopaper may become feasible as a functional substrate in flexible electronics, resulting in paper electronics, printable solar cells and flexible displays that could radically change many aspects of daily life.
Cellulose fibers can easily form many hydrogen bonds. Once broken, the hydrogen bonds can reform on their own-giving the material a 'self-healing' quality. The UMD discovered that the smaller the cellulose fibers, the more hydrogen bonds per square area. This means paper made of very small fibers can both hold together better and re-form more quickly, which is the key for cellulose nanopaper to be both strong and tough.
Read more:
http://www.rdmag.com/news/2015/07/could-stronger-tougher-paper-replace-metal?et_cid=4698497&et_rid=614174443&type=cta
|
Advanced Manufacturing and Related topics
|
Disney research has been up to some 3D printing research I think you'll find pretty interesting: They've been using a method to change material properties throughout a print, without changing the printing medium itself. Take their 3D printed bear, for example: while the bear's head can be hard, its belly can be flexible and its arms can be very bendable, even though the material used to 3D print the bear is the same hard material throughout.
The research team developed a family of microstructures with different elastic properties, allowing designers to employ a specific language to yield these various material properties at will. The team showed off their method by producing a few different toys. One was a teddy bear, one was a rabbit, and they also produced a pair of twin tubes that they said could be used as a manipulator for a soft robot.
"Many functional objects in our everyday life consist of elastic, deformable material, and the material properties are often inextricably linked to function," according to Christian Schumacher,a Ph.D student at ETH Zurich and Disney Research. "3D printing usually involves only a single material or a very small set of materials. However, 3D printing easily produces complex, 3D microstructures which we can use to create metamaterials with properties beyond those of standard printer materials." Schumacher and his colleagues will present their method for controlling elasticity at the upcoming ACM SIGGRAPH 2015, the International Conference on Computer Graphics and Interactive Techniques, taking place in Los Angeles Aug. 9-13. Metamaterials aren't really new, and microstructures can be manipulated in a wide variety of industrial 3D printers, like the Connex series from Stratasys, for example. Varying degrees of microstructures are created through the Objet Studio software, though they are usually spread throughout a few different materials. In this case, the Disney Research team demonstrated the ability to create different metamaterials with the same printing medium, in order to create different elastic regions within an object made from the same material.
Read more:
http://3dprintingindustry.com/2015/08/07/disney-is-manipulating-the-material-properties-of-3d-printed-toys/?utm_source=Facebook&utm_medium=social&utm_campaign=3DPI%2BFacebook
|
|
Lightweight metal matrix syntactic foam between two carbon fabric layers, offering extreme light weight, flexibility, and the ability to withstand deformation and absorb energy. |
A team of researchers reports success in pioneering tests of a layered material with a lightweight metal matrix syntactic foam core that holds significant potential for automobiles, trains, ships and other applications requiring lightweight structural components that retain their strength even when bent or compressed.
The research team of Nikhil Gupta, a New York Univ. (NYU) School of Engineering associate professor in the Dept. of Mechanical and Aerospace Engineering, working with the Toledo, Ohio, company Deep Springs Technology and the U.S. Army Research Laboratory, published their findings in Materials Science and Engineering: A .
Conventional metal foams have gas-filled pores within the metal, which reduce weight but pose some drawbacks, such as difficulty in controlling the size and shape of the pores during manufacturing.
By contrast, metal matrix syntactic foams incorporate porosity in their foam-like structure by means of hollow particles. In recent years there has been an upsurge in the use of these materials, mainly because of their compressive strength. However, bending strength was a limitation for many potential applications, notably automotive structures.
Metallic foams previously have been sandwiched between two stiff sheets, which provide increased flexural strength while the foam core allows the material to withstand large deformation and absorb energy. But Gupta and his colleagues are the first to develop a metal matrix syntactic foam core sandwich composite.
http://www.rdmag.com/news/2015/07/satisfying-hunger-lightweight-yet-strong-material?et_cid=4680272&et_rid=614174443&type=cta
|
The discovery of a previously unknown type of metal deformation-sinuous flow-and a method to suppress it could lead to more efficient machining and other manufacturing advances by reducing the force and energy required to process metals.
Researchers at Purdue Univ. discovered sinuous flow deformation and were surprised to find a potentially simple way to control it, said Srinivasan Chandrasekar, a professor of industrial engineering, who is working with W. Dale Compton, the Lillian M. Gilbreth Distinguished Professor Emeritus of Industrial Engineering, postdoctoral research associate Ho Yeung and graduate student Koushik Viswanathan.
The team discovered the phenomenon by using high-speed microphotography and analysis to study what happens while cutting ductile metals. They found that the metal is deformed into folds while it is being cut-contrary to long-held assumptions that metals are sheared uniformly-and also that sinuous flow can be controlled by suppressing this folding behavior.
"When the metal is sheared during a cutting process it forms these finely spaced folds, which we were able to see for the first time only because of direct observation in real time," Yeung said.
Findings showed the cutting force can be reduced 50% simply by painting metal with a standard marking ink. Because this painted layer was found to suppress sinuous flow, the implications are that not only can energy consumption be reduced by 50% but also that machining can be achieved faster and more efficiently and with improved surface quality, Chandrasekar said.
The findings are detailed in a research paper appearing in Proceedings of the National Academy of Sciences.
"The fact that the metal can be cut easily with less pressure on the tool has significant implications," Compton said. "Machining efficiency is typically limited by force, so it is possible to machine at a much faster rate with the same power."
http://www.rdmag.com/videos/2015/07/twin-discoveries-eerie-effect-may-lead-manufacturing-advances?et_cid=4699640&et_rid=614174443&type=cta
|
While the subject of
white versus green roofs has been debated time and again, there isn't much discussion of how to best cool metal roofs and other structures.
Researchers at Johns Hopkins University's Applied Physics Lab have come up with a solution that not only cools down metal-roofed buildings, but can extend the life of any metal structure from naval ships to playground slides.
"Most paints you use on your car or house are based on polymers, which degrade in the ultraviolet light rays of the sun," says Jason J. Benkoski, Ph.D. "So over time you'll have chalking and yellowing. Polymers also tend to give off volatile organic compounds, which can harm the environment. That's why I wanted to move away from traditional polymer coatings to inorganic glass ones."
Although glass has all of the right properties for cooling and protecting surfaces like light reflection and strength, Benkowski had to find a way around the short-comings of glass -- mainly that it's brittle. He modified potassium silicate to become a compound that when sprayed on a surface is strong and water-resistant. It also expands and contracts with metal surfaces so that it doesn't crack.
Also, because it doesn't contain any organic compounds, it should last far longer than any other paint coatings -- potentially hundreds of years.
http://www.treehugger.com/clean-technology/glass-paint-cools-down-metal-roofs.html
|
Photonic and Electronic Materials & Devices
|
|
Shown here is a prototype laptop power adapter made by Cambridge Electronics using GaN transistors. At 1.5 cubic inches, this is the smallest laptop power adapter ever made. Credit: Cambridge Electronics
|
An exotic material called gallium nitride (GaN) is poised to become the next semiconductor for power electronics, enabling much higher efficiency than silicon.
In 2013, the Department of Energy (DOE) dedicated approximately half of a $140 million research institute for power electronics to GaN research, citing its potential to reduce worldwide energy consumption. Now MIT spinout Cambridge Electronics Inc. (CEI) has announced a line of GaN transistors and power electronic circuits that promise to cut energy usage in data centers, electric cars, and consumer devices by 10 to 20 percent worldwide by 2025.
Power electronics is a ubiquitous technology used to convert electricity to higher or lower voltages and different currents-such as in a laptop's power adapter, or in electric substations that convert voltages and distribute electricity to consumers. Many of these power-electronics systems rely on silicon transistors that switch on and off to regulate voltage but, due to speed and resistance constraints, waste energy as heat.
CEI's GaN transistors have at least one-tenth the resistance of such silicon-based transistors, according to the company. This allows for much higher energy-efficiency, and orders-of-magnitude faster switching frequency-meaning power-electronics systems with these components can be made much smaller. CEI is using its transistors to enable power electronics that will make data centers less energy-intensive, electric cars cheaper and more powerful, and laptop power adapters one- third the size-or even small enough to fit inside the computer itself.
"This is a once-in-a-lifetime opportunity to change electronics and to really make an impact on how energy is used in the world," says CEI co-founder Tomás Palacios, an MIT associate professor of electrical engineering and computer science who co-invented the technology.
Read more at:
http://phys.org/news/2015-07-silicon-gallium-nitride-electronics-drastically.html#jCp
Read more:
http://phys.org/news/2015-07-silicon-gallium-nitride-electronics-drastically.html
|
Researchers at the Univ. of Maryland (UMD) recently discovered that paper made of cellulose fibers is tougher and stronger the smaller the fibers get. For a long time, engineers have sought a material that is both strong (resistant to non-recoverable deformation) and tough (tolerant of damage).
"Strength and toughness are often exclusive to each other," said Teng Li, associate professor of mechanical engineering at UMD. "For example, a stronger material tends to be brittle, like cast iron or diamond."
The UMD team pursued the development of a strong and tough material by exploring the mechanical properties of cellulose, the most abundant renewable bio-resource on Earth. Researchers made papers with several sizes of cellulose fibers-all too small for the eye to see-ranging in size from about 30 um to 10 nm. The paper made of 10-nm-thick fibers was 40 times tougher and 130 times stronger than regular notebook paper, which is made of cellulose fibers a thousand times larger.
"These findings could lead to a new class of high performance engineering materials that are both strong and tough, a Holy Grail in materials design," said Li.
High-performance yet lightweight cellulose-based materials might one day replace conventional structural materials (metals) in applications where weight is important. This could lead, for example, to more energy-efficient and "green" vehicles. In addition, team members say, transparent cellulose nanopaper may become feasible as a functional substrate in flexible electronics, resulting in paper electronics, printable solar cells and flexible displays that could radically change many aspects of daily life.
Cellulose fibers can easily form many hydrogen bonds. Once broken, the hydrogen bonds can reform on their own-giving the material a 'self-healing' quality. The UMD discovered that the smaller the cellulose fibers, the more hydrogen bonds per square area. This means paper made of very small fibers can both hold together better and re-form more quickly, which is the key for cellulose nanopaper to be both strong and tough.
Electrochromic glass essentially uses electric charge to switch a window from allowing sunlight in to blocking it out. Some have estimated that such "smart windows" could cut lighting needs by about 20 percent and the cooling load by 25 percent at peak times.
Now researchers at the University of Texas Austin have found a way to make them even better. They developed a novel nanostructure architectcure for electrochromic materials that enables a highly selective cool mode and warm mode-something thought to be impossible a few years back.
In research published in the journal Nano Letters, the University of Texas researchers along with scientists at Lawrence Berkeley National Laboratory were able to get nanostructured electrochromic materials to control 90 percent of the near-infrared (NIR) light and 80 percent of the visible light. What's more, it only requires a few minutes to switch between these two modes, whereas previously reported materials took hours to make this transition.
"We believe our new architected nanocomposite could be seen as a model material, establishing the ideal design for a dual-band electrochromic material," said Delia Milliron, a professor at the University of Texas who led the research, in a press release. "This material could be ideal for application as a smart electrochromic window for buildings."
The researchers were able to achieve the faster switching by creating a porous interpenetrating network in a two-component composite material. The architecture of this network created channels, through which electronic and ionic changes could propagate.
Read more:
http://spectrum.ieee.org/nanoclast/green-tech/conservation/nanostructured-glass-controls-light-and-reduces-energy-costs/?utm_source=energywise&utm_medium=email&utm_campaign=072915
|
|
Samples of the new hybrid sol-gel material are shown placed on a clear plastic substrate for testing. Credit: John Toon, Georgia Tech
|
Using a hybrid silica sol-gel material and self-assembled monolayers of a common fatty acid, researchers have developed a new capacitor dielectric material that provides an electrical energy storage capacity rivaling certain batteries, with both a high energy density and high power density.
If the material can be scaled up from laboratory samples, devices made from it could surpass traditional electrolytic capacitors for applications in electromagnetic propulsion, electric vehicles and defibrillators. Capacitors often complement batteries in these applications because they can provide large amounts of current quickly.
The new material is composed of a silica sol-gel thin film containing polar groups linked to the silicon atoms and a nanoscale self-assembled monolayer of an octylphosphonic acid, which provides insulating properties. The bilayer structure blocks the injection of electrons into the sol-gel material, providing low leakage current, high breakdown strength and high energy extraction efficiency.
"Sol-gels with organic groups are well known and fatty acids such as phosphonic acids are well known," noted Joseph Perry, a professor in the School of Chemistry and Biochemistry at the Georgia Institute of Technology. "But to the best of our knowledge, this is the first time these two types of materials have been combined into high-density energy storage devices."
The research, supported by the Office of Naval Research and the Air Force Office of Scientific Research, was reported July 14 in the journal Advanced Energy Materials.
The need for efficient, high-performance materials for electrical energy storage has been growing along with the ever-increasing demand for electrical energy in mobile applications. Dielectric materials can provide fast charge and discharge response, high energy storage, and power conditioning for defense, medical and commercial applications. But it has been challenging to find a single dielectric material able to maximize permittivity, breakdown strength, energy density and energy extraction efficiency.
Read more:
http://phys.org/news/2015-07-sol-gel-capacitor-dielectric-record-high-energy.html
|
|
Researchers at Oxis Energy in England could be poised to commercialize lithium-sulfur batteries within the next few years. Image: Oxis Energy |
Lithium-ion batteries remain the technology-of-choice for today's crop of electric cars, but challengers are revving up to try to upset the current order. An article in Chemical & Engineering News (C&EN) takes a look at two of the top contenders vying to erode lithium-ion's dominance.
Alex Scott, a senior editor at C&EN, reports on two developments from companies in England that seem poised to compete in the electric car battery market within the next two to four years. One is a sodium-ion version, produced by a start-up called Faradion. The other is a battery powered by lithium-sulfur technology and is being developed by Oxis Energy. Both companies assert their advances will be able to compete with lithium-ion in performance, safety and costs.
Some industry watchers, however, remain unconvinced by the claims, given that a slew of other battery-makers made similar promises and then failed to deliver. Soon enough, the fates of Faradion and Oxis could also be determined. Faradion has set a goal to match the energy density of lithium-ion batteries by 2017. And although they're still dealing with battery cycle issues, Oxis' lithium-sulfur technology has already attracted the attention of the military.
http://www.acs.org/content/acs/en/pressroom/presspacs/2015/acs-presspac-july-22-2015/new-battery-technologies-take-on-lithium-ion.html?
|
|
This artistic rendering of a computer simulation shows the formation of a liquid-like particle during the early stages of calcium carbonate crystallization. Image: Adam F. Wallace/Univ. of Delaware and David J. Carey |
Scientists have long worked to understand how crystals grow into complex shapes. Crystals are important in materials from skeletons and shells to soils and semiconductor materials, but much is unknown about how they form.
Now, an international group of researchers has shown how nature uses a variety of pathways to grow crystals that go beyond the classical, one-atom-at-a-time route.
The findings, published in Science, have implications for decades-old questions in science and technology such as how animals and plants grow minerals into shapes that have no relation to their original crystal symmetry. Or why some contaminants are so difficult to remove from stream sediments and groundwater.
"Researchers across all disciplines have made observations of skeletons and laboratory-grown crystals that cannot be explained by traditional theories," said Patricia Dove, a University Distinguished Professor at Virginia Tech and the C.P. Miles Professor of Science in the College of Science. "We show how these crystals can be built up into complex structures by attaching particles-as nanocrystals, clusters, or droplets-that become organized into complex shapes. Many scientists have contributed to identifying these particles and pathways to becoming a crystal-our challenge was to put together a framework to understand them."
The results emerged from discussions among 15 scientists working in the fields of geochemistry, physics, biology, and the earth and materials sciences, including at the U.S. Dept. of Energy (DOE)'s Pacific Northwest National Laboratory. At home, these researchers conduct lab experiments, investigate animal skeletons, study soils and streams, or use computer simulations to visualize how particles can form and attach.
http://www.rdmag.com/news/2015/08/new-insight-how-crystals-form?et_cid=4709660&et_rid=614174443&type=cta
|
|
A sample of the composite metal foam developed in Rabiei's research group. Photo credit: Afsaneh Rabiei. |
Research from North Carolina State University shows that lightweight composite metal foams are effective at blocking X-rays, gamma rays and neutron radiation, and are capable of absorbing the energy of high impact collisions. The finding means the metal foams hold promise for use in nuclear safety, space exploration and medical technology applications.
"This work means there's an opportunity to use composite metal foam to develop safer systems for transporting nuclear waste, more efficient designs for spacecraft and nuclear structures, and new shielding for use in CT scanners," says Afsaneh Rabiei, a professor of mechanical and aerospace engineering at NC State and corresponding author of a paper on the work.
Rabiei first developed the strong, lightweight metal foam for use in transportation and military applications. But she wanted to determine whether the foam could be used for nuclear or space exploration applications - could it provide structural support, protect against high impacts and provide shielding against various forms of radiation?
To that end, she and her colleagues conducted multiple tests to see how effective it was at blocking X-rays, gamma rays and neutron radiation. She then compared the material's performance to the performance of bulk materials that are currently used in shielding applications. The comparison was made using samples of the same "areal" density - meaning that each sample had the same weight, but varied in volume.
The most effective composite metal foam against all three forms of radiation is called "high-Z steel-steel" and was made up largely of stainless steel, but incorporated a small amount of tungsten. However, the structure of the high-Z foam was modified so that the composite foam that included tungsten was not denser than metal foam made entirely of stainless steel.
The researchers tested shielding performance against several kinds of gamma ray radiation. Different source materials produce gamma rays with different energies. For example, cesium and cobalt emit higher-energy gamma rays, while barium and americium emit lower-energy gamma rays.
The researchers found that the high-Z foam was comparable to bulk materials at blocking high-energy gamma rays, but was much better than bulk materials - even bulk steel - at blocking low-energy gamma rays.
Similarly, the high-Z foam outperformed other materials at blocking neutron radiation.
https://news.ncsu.edu/2015/07/rabiei-foam-rays-2015/?
|
Thermoelectric modules based on polymers offer multiple advantages, including being printable, flexible, operating at moderate temperatures, and avoiding rare or toxic elements. They are also able to redistribute heat - a constant problem with current electronics.
But thermoelectric modules require semiconductor pairs to transport holes and electrons separately. Finding a suitable polymer for electron transport, or one which can be doped in order to make it suitable, is a challenge.
Researchers from the USA have now fabricated a purely n-type polymer semiconductor composite for electron transport. They combine a pyromellitic diimide polymer which has pentafluorophenyl end caps with an in situ-crystallized inorganic component, SnCl2, chosen for its well-known reduction ability. This solid additive increases the electron-carrying capacity and the voltage that can be obtained from the temperature difference. The mechanism is a combination of electron donation to the polymer and surface electroni c effects.
They compare their polymer with current commercial polymer systems, and find that their voltage per unit temperature breaks the current record for n-type polymers.
Advanced Science is a new journal from the team behind Advanced Materials, Advanced Functional Materials, and Small. The journal is fully Open Access and is free to read now at www.advancedscience.com.
http://www.materialsviews.com/polymer-thermoelectrics/?utm_source=MaterialsViews+subscribers&utm_campaign=2ec461193a-weekly_newsletter_campaign&utm_medium=email&utm_term=0_ae9549257a-2ec461193a-45343933
|
|
A scanning tunneling electron micrograph (STEM) of the polymer material shows its division into crystalline regions (light areas of orderly dots) and the amorphous, disordered matrix, which is seen as the dark background. The original 2-D STEM views were rendered into 3-D form to create this visualization. Image: Asli Ugur |
Materials known as conjugated polymers have been seen as very promising candidates for electronics applications, including capacitors, photodiodes, sensors, organic light-emitting diodes and thermoelectric devices. But they've faced one major obstacle: Nobody has been able to explain just how electrical conduction worked in these materials, or to predict how they would behave when used in such devices.
Now researchers at Massachusetts Institute of Technology (MIT) and Brookhaven National Laboratory have explained how electrical charge carriers move in these compounds, potentially opening up further research on such applications. A paper presenting the new findings is published in Advanced Materials.
Conjugated polymers fall somewhere between crystalline and amorphous materials-and that's caused some of the difficulty in explaining how they work, says Asli Ugur, an MIT postdoc and lead author of the paper. Crystals have a perfectly regular arrangement of atoms and molecules, while amorphous materials have a completely random arrangement. But conjugate polymers have some of both characteristics: regions of orderly arrangement, mixed randomly with regions of complete disorder.
"Some models have tried to explain how these materials behave, but there's been no direct evidence," Ugur says, for which model matches the reality. "Here, we've shown that the effect of crystallite size"-the sizes of the ordered domains within the material-plays a crucial role.
That's because the trickiest part of conduction in such materials is what happens when charge carriers-in this case ions, or electrically charged atoms-reach the edge of one type of domain and have to "hop" into the next.
In bulk materials, those ions can go in any direction. But in this polymer, which can be very thin, there are fewer neighboring crystalline domains to which an ion can hop. With fewer options, conduction is more efficient, Ugur says, adding that, "As you get thinner, the conditions [for conduction] improve, even though the material didn't change."
http://newsoffice.mit.edu/2015/solving-mysteries-conductivity-polymers-0714?
|
|
Images of the microgears and experimental setup. Credit: Maggi, et al. ©2015 Nature Communications |
(Phys.org)-Scientists have demonstrated that pinwheel-shaped microgears floating on a liquid surface can rotate at speeds of up to 300 r.p.m. when illuminated by an ordinary LED. This light-driven motion, which arises because the light creates a tiny temperature difference and, subsequently, a surface tension difference in the surrounding fluid, is about five orders of magnitude more efficient than other mechanisms that convert light into work. As the effect is not size-dependent, the scientists expect that the system could be scaled to both the macroscale and the nanoscale.
The researchers, Claudio Maggi and coauthors from the University of Rome, the Italian Institute of Technology in Genova, and the NANOTEC-CNR Institute of Nanotechnology in Rome, have published a paper on the new demonstration of light-to-work conversion in a recent issue of Nature Communications.
In their study, the scientists fabricated the microgears using laser lithography, coated them with a layer of amorphous carbon to increase light absorption, and immersed them in a liquid. They then deposited a small drop of the gear-containing liquid onto a microscope glass slide and illuminated it with an LED. While previous light-driven motors generally require high-power laser beams to induce motion, here the wide-field LED could induce motion with just a few microwatts of power per gear, corresponding to a 100,000 times higher light-to-work
conversion efficiency.
The reason for the increase in efficiency is that the new system operates under an entirely different light-to-work conversion mechanism. Previously, similar systems have relied on either the radiation pressured exerted by highly focused laser beams, or on thermophoresis, which is the slow migration of solid particles induced by thermal gradients in the surrounding fluid. To achieve thermophoresis, half of the particle is covered in a heat-absorbing coating, so that when exposed to strong illumination, the particle will be propelled along a temperature gradient.
http://phys.org/news/2015-08-tiny-gears-light-to-work-conversion-efficiency.html
|
Microstructured Thin FIlms and Coatings
|
Liquid deposition processes are very versatile methods to produce sub-micron homogeneous coatings through spreading of a solution onto a substrate and evaporation of the volatile compounds. They are seen as serious alternatives to dry deposition techniques, such as physical vapor deposition (PVD) chemical vapor deposition (CVD) or plasma-enhanced CVD (PECVD), because they permit endless of chemical combinations to be processed with an excellent control of the inner layer structure and thickness, and with manufacturing rapidity and cost efficiency.
Amongst the various available techniques some are already commonly used in R&D and production, such as dip coating and spin coating. Dip coating is considered as the best technique to precisely and simultaneously control the thickness, the internal (nano)structure, with the highest homogeneity. However, it usually requires a large amount of coating solution to ensure complete immersion of substrates, making it impractical when the solution is unstable and/or hazardous, or contains scare and expensive materials. For such reasons, spin coating is often much more in favor over dip coating, despite the fact that most of the solution is wasted during the former process.
Having worked in the field of liquid deposition processes for the last 20 years, David Grosso has always been motivated to find a new way that combines the high control, the best homogeneity, and the chemical versatility associated to dip-coating with the possibility to coat a single face of a relatively large area substrate with a minimum of solution, and with no waste. Now, D. Grosso and his collaborators M. Faustini and D. Ceratti at Sorbonne Universités and Aix-Marseille Université (both in France) have achieved this goal by developing
A New Dip Coating Method to Obtain Large-Surface Coatings with a Minimum of Solution.
The "bi-phasic" concept is rather simple yet very creative. The researchers introduce an immiscible, heavy, and inert liquid to fill most of the volume of the reservoir before adding the coating solution, and therefore, only a small amount of coating solution is needed to cover the surface of the bottom layer. The substituting phase can be perfluoroalkanes or liquid metals (gallium or mercury) so that the affinity between this phase and the substrate is minimized. In fact, the contact angle at the triple-phase line will be too high to enable any coating by the substituting phase.
Read more:
http://www.materialsviews.com/game-changer-dip-coating-less-please-hold-adma-201502518/?utm_source=MaterialsViews+subscribers&utm_campaign=9dd2722048-weekly_newsletter_campaign&utm_medium=email&utm_term=0_ae9549257a-9dd2722048-45343933
|
Evanston, IL | Posted on August 18th, 2015The research team is the first to identify the ideal "roughness" needed in the texture of a surface to keep it dry for a long period of time when submerged in water. The valleys in the surface roughness typically need to be less than one micron in width, the researchers found. That's really small -- less than one millionth of a meter -- but these nanoscopic valleys have macroscopic impact.
Understanding how the surfaces deflect water so well means the valuable feature could be reproduced in other materials on a mass scale, potentially saving billions of dollars in a variety of industries, from antifouling surfaces for shipping to pipe coatings resulting in lower drag. That's science and engineering, not serendipity, at work for the benefit of the economy.
"The trick is to use rough surfaces of the right chemistry and size to promote vapor formation, which we can use to our advantage," said Neelesh A. Patankar, a theoretical mechanical engineer who led the research.
"When the valleys are less than one micron wide, pockets of water vapor or gas accumulate in them by underwater evaporation or effervescence, just like a drop of water evaporates without having to boil it. These gas pockets deflect water, keeping the surface dry," he said.
In a study published today (Aug. 18) by the journal Scientific Reports, Patankar and his co-authors explain and demonstrate the nanoscale mechanics behind the phenomenon of staying dry underwater.
In their experiments, the researchers used a variety of materials with and without the key surface roughness and submerged them in water. Samples with the nanoscale roughness remained dry for up to four months, the duration of the experiment. Other samples were placed in harsh environments, where dissolved gas was removed from the ambient liquid, and they also remained dry.
"It was amazing and what we were hoping for," said Patankar, a professor of mechanical engineering in the McCormick School of Engineering and Applied Science. "My lab likes to defy normal experience. In this work, we looked for properties that manipulate the water phase changes we know."
The researchers also report that nature uses the same strategy of surface roughness in certain aquatic insects, such as water bugs and water striders. Small hairs on the surfaces of their body have the less-than-one-micron spacing, allowing gas to be retained between the hairs.
"These gas-retaining insects have surface properties consistent with our predictions, allowing them to stay dry for a long time," said Paul R. Jones, the study's first author. He is a Ph.D. student in Patankar's research group.
The researchers focused on the nanoscopic structure of surfaces, which, at the nanoscale, are somewhat akin to the texture of a carpet, with tiny spike-like elevations separated by valley-shaped pores in between.
When submerged, water tends to cling to the top of the spikes, while air and water vapor accrue in the pores between them. The combination of trapped air and water vapor within these cavities forms a gaseous layer that deters moisture from seeping into the surface below.
"When we looked at the rough surfaces under the microscope, we could see clearly the vacant gaps -- where the protective water vapor is," Patankar said.
http://www.nanotech-now.com/news.cgi?story_id=52109
|
Characterization of Advanced Materials
|
The discovery of a fiber-reinforced, concrete-like rock formed in the depths of a dormant supervolcano in Italy could help explain the unusual ground swelling that led to the evacuation of an Italian port city in recent years, and may inspire the creation of durable building materials in the future, Stanford Univ. scientists say.
The "natural concrete" at the Campi Flegrei volcano near Naples is similar to Roman concrete, a legendary compound invented by the Romans and used to construct the Pantheon, the Coliseum and ancient shipping ports throughout the Mediterranean.
"This implies the existence of a natural process in the subsurface of Campi Flegrei that is similar to the one that is used to produce concrete," said Tiziana Vanorio, an experimental geophysicist at the Stanford School of Earth, Energy & Environmental Sciences.
Campi Flegrei lies at the center of a large depression, or caldera, that is pockmarked by craters formed during past eruptions, the last of which occurred nearly 500 years ago. Nestled within this caldera is the colorful port city of Pozzuoli, which was founded in 600 B.C. by the Greeks.
Beginning in 1982, the ground beneath Pozzuoli began rising at an alarming rate. Within a two-year span, the uplift exceeded 6 feet-an amount unprecedented anywhere in the world. "The rising sea bottom rendered the Bay of Pozzuoli too shallow for large craft," Vanorio said.
http://www.rdmag.com/videos/2015/07/volcanic-rocks-resembling-roman-concrete-help-solve-mystery?et_cid=4672003&et_rid=614174443&type=cta
|
Thinking of NMR brings to mind large machines with superconducting magnets. One finds them in chemical research institutions to unravel molecular structures and in hospitals to measure images through soft tissue. But small machines exist that are portable and suitable for materials testing at the site of the object.
Teymouri, Kwamen and Blümich from RWTH Aachen University have studied the degradation of factory-grade LDPE (low-density polyethylene) pellets when exposed to air at different temperatures with a desktop NMR machine that uses a compact, permanent magnet and is maintenance-free. This user-friendly device delivers NMR relaxation data, which report the concentration and mobility of the crystalline, interfacial and amorphous domains of the semi-crystalline polymer and their changes with progressive aging.
According to the researchers, sample preparation and measurement are simple and fast, and their NMR observations are in agreement with more demanding DSC, FTIR, and SEC measurements. During the aging process, crystallization and chemical degradation progress at different rates. While at temperature below 90° C crystallization dominates, oxidative degradation takes over after 28 days when aging at 100° C. LDPE degrades chemically by crosslinking and chains scission, whereby chain scission dominates at long aging times.
However, in addition to time and temperature, the molecular weight distribution plays a role in the aging process. In nearly all factory-grade polymer materials a considerable fraction of oligomers and low-molecular weight polymers is contained as wax. Their NMR data reveal that the wax content can accelerate the aging process and increase the crystallinity during thermal aging.
http://www.materialsviews.com/nmr-detective-investigating-ldpe-degradation/?utm_source=MaterialsViews+subscribers&utm_campaign=42b011f973-weekly_newsletter_campaign&utm_medium=email&utm_term=0_ae9549257a-42b011f973-45343933
|
Common sense tells that an object will always shrink in all three dimensions when it is subject to an increased hydrostatic pressure. However, as counterintuitive as it may sound, there do indeed exist such materials, albeit rather rare, that can expand along two directions even when a compressive force is applied to all three dimensions. This novel mechanical behavior, termed as negative area compressibility (NAC), while challenging our sense of the basic laws of physics, actually shows interesting potentials in many scientific and technical fields, such as ultra-sensitive pressure sensors, optical telecommunication, shock absorbing materials, and even novel body armors - imagine Tony Stark comes back with one in Iron Man 4. However, up until now, only six materials, four organic and two inorganic, have been found to possess NAC.
Now, Zheshuai Lin, Xingxing Jiang at Technical Institute of Physics and Chemistry, Chinese Academy of Sciences (Beijing), collaborating with Wei Li at Huazhong University of Science and Technology (Wuhan) and co-workers, reveal the
NAC property in potassium beryllium fluoroborate (KBBF) by high-pressure synchrotron powder X-ray diffraction experiments combined with first-principles calculations, adding a new member to the small family of materials.
The NAC behavior often originates from the strongly anisotropic atomic arrangements in the microscopic structure. For a long time, borates have been extensively studied mainly due to their excellent optical properties, especially large nonlinear optical (NLO) effects, in the ultraviolet (UV, wavelength < 400 nm) and deep-UV (wavelength < 200 nm) regions, corresponding to strong anisotropy in their crystal structures. In particular, as a deep-UV NLO material, KBBF features very anisotropic structure: its framework is built by two dimensional infinite anionic layers that are perpendicular to the c-axis.
The researchers find that KBBF exhibits a NAC behavior over a pressure range from 0.22 to 6.39 GPa, by far the broadest among all known NAC materials. Moreover, the NAC behavior is completely isotropic in the ab plane due to the uniaxial crystal symmetry. The mechanism analysis reveals that the significant shrinkage of the 'soft' Be-F bond along the c-axis, when hydrostatically compressed, results in the orthogonal expansion of the O3 plane in the (BeO3F)5- tetrahedra, giving rise to NAC along the ab plane.
The present findings make KBBF the first completely isotropic NAC material that can transmit deep-UV light. In addition to the NAC effect, the authors have also predicted for KBBF extremely large Poisson's ratios and very high acoustic-optical figure of merit. Its very large bandgap allows KBBF to find applications as the strain-converting material used in intrinsic fiber Fabry-Perot interferometer pressure sensor with ultra-fine pressure-sensing sensitivity or as the excellent acoustic-optics diffracting devices in the high-precision ultrasonically driven deep-UV light modulators and scanners.
Read more:
http://www.materialsviews.com/tougher-tough-borate-expands-pressure-please-hold-adma-201502212/?utm_source=MaterialsViews+subscribers&utm_campaign=9dd2722048-weekly_newsletter_campaign&utm_medium=email&utm_term=0_ae9549257a-9dd2722048-45343933
|
A researcher now at the Univ. of Central Florida has developed a new method for identifying materials' unique chemical "fingerprints" and mapping their chemical properties at a much higher spatial resolution than ever before.
It's a discovery that could have promising implications for fields as varied as biofuel production, solar energy, opto-electronic devices, pharmaceuticals and medical research.
"What we're interested in is the tools that allow us to understand the world at a very small scale," said UCF professor Laurene Tetard, formerly of the Oak Ridge National Laboratory. "Not just the shape of the object, but its mechanical properties, its composition and how it evolves in time."
For more than two decades, scientists have used atomic force microscopy-a probe that acts like an ultra-sensitive needle on a record player-to determine the surface characteristics of samples at the microscopic scale. A "needle" that comes to an atoms-thin point traces a path over a sample, mapping the surface features at a sub-cellular level.
But that technology has its limits. It can determine the topographical characteristics of a sample, but it can't identify its composition. And with the standard tools currently used for chemical mapping, anything smaller than roughly half a micron is going to look like a blurry blob, so researchers are out of luck if they want to study what's happening at the molecular level.
A team led by Tetard has come up with a hybrid form of that technology that produces a much clearer chemical image. As described in Nature Nanotechnology, Hybrid Photonic-Nanomechanical Force Microscopy (HPFM) can discern a sample's topographic characteristics together with the chemical properties at a much finer scale.
The HPFM method is able to identify materials based on differences in the vibration produced when they're subjected to different wavelengths of light-essentially a material's unique "fingerprint."
Read more:
http://www.rdmag.com/news/2015/08/vibrations-identify-materials-composition?et_cid=4733294&et_rid=614174443&type=cta
|
Biomaterials and Biotechnology
|
|
An artificial analogue of the water channel protein, aquaporin, was shown to have permeabilities approaching that of aquaporins and carbon nanotubes. They also arrange in tight 2-D arrays. Image: Karl Decker/Univ. of Illinois at Urbana-Champaign, and Yuexiao Shen /Penn State |
A synthetic membrane that self-assembles and is easily produced may lead to better gas separation, water purification, drug delivery and DNA recognition, according to an international team of researchers.
This biomimetic membrane is composed of lipids-fat molecules-and protein-appended molecules that form water channels that transfer water at the rate of natural membranes, and self-assembles into 2-D structures with parallel channels.
"Nature does things very efficiently and transport proteins are amazing machines present in biological membranes," said Manish Kumar, assistant professor of chemical engineering, Penn State. "They have functions that are hard to replicate in synthetic systems."
The researchers developed a second-generation synthetic water channel that improves on earlier attempts to mimic aquaporins-natural water channel proteins-by being more stable and easier to manufacture. The peptide-appended pillar[5]arenes (PAP) are also more easily produced and aligned than carbon nanotubes, another material under investigation for membrane separation. Kumar and co-authors report their development in the Proceedings of the National Academy of Science.
"We were surprised to see transport rates approaching the 'holy grail' number of a billion water molecules per channel per second," said Kumar. "We also found that these artificial channels like to associate with each other in a membrane to make 2-D arrays with a very high pore density."
The researchers consider that the PAP membranes are an order of magnitude better than the first-generation artificial water channels reported to date. The propensity for these channels to automatically form densely packed arrays leads to a variety of engineering applications.
"The most obvious use of these channels is perhaps to make highly efficient water purification membranes," said Kumar.
Read more:
http://www.rdmag.com/news/2015/07/self-assembling-biomimetic-membranes-may-aid-water-filtration?et_cid=4704781&et_rid=614174443&type=cta
|
|
A paraffin wax capsule developed by researchers at MIT is shown next to a penny. Image: Aaron C. Sather |
Chemists working in a variety of industries and fields typically go through a laborious process to measure and mix reagents for each reaction they perform. And many of the common reagents they use sit for months or years on shelves in laboratories, where they can react with oxygen and water in the atmosphere, rendering them useless.
In a paper published in Nature, researchers at Massachusetts Institute of Technology (MIT) describe a technique that could help avoid this costly waste, and greatly reduce the number of steps a chemist must perform to prepare common compounds for use in a wide range of chemical transformations.
Aaron C. Sather, the lead author of the paper, is a postdoc in the lab of Stephen Buchwald, the Camille Dreyfus Professor in Chemistry. He and his colleagues have harnessed the power of a small, simple technology that could transform the benchtop practice of organic chemistry: the capsule.
Some labs use what is known as a "glove box," an inert container that permits researchers to manipulate reagents in a controlled environment, isolated from the oxygen, carbon dioxide, and water in ambient air. But many laboratories in industry and academia don't have glove boxes because they're expensive to maintain, and take up precious space, Sather says. As a result, many chemists avoid performing certain useful, but complicated, reactions because they require a glove box.
Many reagents and catalysts aren't used simply because of this inconvenience. What's more, for a bench chemist working in materials science or pharmaceuticals, performing the complex sequence of steps to prepare certain compounds may be unfamiliar and onerous.
"If you can grab the reagents off the shelf and get the reaction to work without that expertise or a glove box, it's much more accessible," Sather says.
Read more:
http://www.rdmag.com/news/2015/08/researchers-pioneer-use-capsules-save-materials?et_cid=4738827&et_rid=614174443&type=cta
|
When you spill a bit of water onto a tabletop, the puddle spreads-and then stops, leaving a well-defined area of water with a sharp boundary.
There's just one problem: The formulas scientists use to describe such a fluid flow say that the water should just keep spreading endlessly. Everyone knows that's not the case-but why?
This mystery has now been solved by researchers at MIT-and while this phenomenon might seem trivial, the finding's ramifications could be significant: Understanding such flowing fluids is essential for processes from the lubrication of gears and machinery to the potential sequestration of carbon dioxide emissions in porous underground formations.
The new findings are reported in the journal Physical Review Letters in a paper by Ruben Juanes, an associate professor of civil and environmental engineering, graduate student Amir Pahlavan, research associate Luis Cueto-Felgueroso, and mechanical engineering professor Gareth McKinley.
"The classic thin-film model describes the spreading of a liquid film, but it doesn't predict it stopping," Pahlavan says. It turns out that the problem is one of scale, he says: It's only at the molecular level that the forces responsible for stopping the flow begin to show up. And even though these forces are minuscule, their effect changes how the liquid behaves in a way that is obvious at a much larger scale.
http://phys.org/news/2015-07-puddles-simple-everyday-phenomenon-unexplained.html#nRlv
|
|
From left: Peter Facchini, professor in biological sciences, Jill Hagel, research associate, and Scott Farrow, PhD student. They have characterized a novel gene that encodes the gateway enzyme in the formation of morphine and begun to understand how poppies synthesize the pain killing enzymes. Credit: Riley Brandt, University of Calgary |
Many people who live in developing countries do not have access to the pain relief that comes from morphine or other analgesics. That's because opiates are primarily derived from the opium poppy plant (Papaver somniferum) and are dependent on the plant health and supply around the world.
After years of leading research on the opium poppy, University of Calgary scientists, Peter Facchini, his PhD student, Scott Farrow, and research associate Jill Hagel, have characterized a novel gene that encodes the gateway enzyme in the formation of morphine -which is to say, they've begun to understand how poppies synthesize the pain killing enzymes. The discovery opens the door to alternative production systems, aside from the plant itself.
Farrow, who is building on the insights Facchini and his team have been gathering over more than 23 years of research into opium poppies, is the lead author of a new paper that describes one of many significant discoveries arising from Facchini's research program.
"The gene we've isolated actually consists of a natural fusion between two ancestral genes, which encodes the gateway enzyme in the formation of morphine," says Farrow. "It's really interesting to see these fused genes in a metabolic pathway. It provides us with a new tool to search for something missing in other plants as well."
The findings were published July 1 in Nature Chemical Biology, and detail the missing step to morphine biosynthesis.
http://phys.org/news/2015-07-opium-poppies-morphine.html
|
|
This graphic depicts the exoskeleton structure of a certain type of deep-sea shrimp able to survive the scalding hot waters of hydrothermal vents thousands of feet under water. Insights into the complex molecular behavior of the materials could have implications for the design of new synthetic armor capable of withstanding environmental extremes. (Purdue University photo/Tao Qu) |
WEST LAFAYETTE, Ind. - New research is revealing details about how the exoskeleton of a certain type of deep-sea shrimp allows the animal to survive scalding hot waters in hydrothermal vents thousands of feet under water.
"A biological species surviving in that kind of extreme environment is a big deal," said Vikas Tomar, an associate professor in Purdue University's School of Aeronautics and Astronautics. "And shrimp are a great test case for evolution because you can find different species all over the world living at various depths and with a range of adaptation requirements."
Tomar and doctoral students Tao Qu, Devendra Verma, Yang Zhang and Chandra Prakash compared the exoskeletons of the deep-sea shrimp Rimicaris exoculata and the shallow-dwelling shrimp Pandalus platyceros. The deep-sea species lives 2,000 meters below the ocean surface in volcanic hydrothermal vents where temperatures can exceed 400 degrees Celsius, whereas the other species lives just below the ocean surface.
"We want to understand how evolution affects material behavior in the exoskeletons of these two shrimp species that thrive in far different conditions," Tomar said.
Insights into the complex molecular behavior of the materials could have implications for the design of new synthetic armor capable of withstanding environmental extremes.
New findings were detailed in a research paper published online July 2 and will appear in a future print issue of the journal Acta Biomaterialia. Two other recent papers by the same researchers focused on laboratory experiments into the shrimp exoskeletons.
http://www.purdue.edu/newsroom/releases/2015/Q3/advanced-composites-may-borrow-designs-from-deep-sea-shrimp.html?
|
AZO dyes, generated from industrial waste (especially textile industries), create an alarming threat as toxic water pollutants and carcinogens. Recent studies show that AZO dyes decrease the
permeability of the blood-brain barrier, which may result in chronic neurological diseases including stroke and neuro-inflammatory disorders. Traditionally, pure transition metals, noble metals (such as platinum and palladium), and carbon-based materials are used to degrade and detoxify different organic water pollutants including AZO dyes. However, high cost and susceptibility to catalyst poisoning limit the application of these traditional materials as water purifier.
In this study by S. Mukherjee et al. from the University of North Texas, large surface area metallic glass particles were used for rapid dissociation of AZO dye, demonstrating the potential use of these novel materials for treating a variety of toxic organic dyes. Aluminum-based metallic glass of composition Al82Y8Ni7Fe3 was found to completely degrade AZO dye at room temperature without any toxic by-products. The dye degradation rate and catalytic activity were characterized by UV-VIS absorption spectroscopy. In addition, by combining different spectroscopy techniques, the dye dissociation mechanism was identified to be a bi-functional surface catalysis process involving the transition metals in the alloy. Charge transfer from simultaneous ionization of the transition metals (iron and nickel) help in dissociating the unsaturated bonds of the AZO dye in an aqueous medium. The amorphous nature of the alloy renders it inert and durable during the reaction, while promoting high surface catalytic activity at the same time. This has the potential of creating a wide range of applications, including high performance catalysis, water purification, and chemical conversion.
http://www.materialsviews.com/degradation-toxic-water-pollutants-catalytic-amorphous-metals/?utm_source=MaterialsViews+subscribers&utm_campaign=2ec461193a-weekly_newsletter_campaign&utm_medium=email&utm_term=0_ae9549257a-2ec461193a-45343933
|
|
Pulsed near-infrared light (red) is shone onto a tumor (white) that is encased in blood vessels. The tumor is imaged by multispectral optoacoustic tomography via the ultrasound emission (blue) from the gold nanotubes. (Image courtesy of Jing Claussen, Ithera Medical, Germany) |
Scientists at the University of Leeds in England have shown that gold nanotubes can serve as internal nanoprobes for high-resolution multispectral imaging, as drug delivery vehicles, and as agents for destroying cancer cells. In their study, they demonstrated biomedical utility of gold nanotubes in a mouse model of human cancer.
"High recurrence rates of tumors after surgical removal remain a formidable challenge in cancer therapy," explains Dr. Sunjie Ye, who is based in both the School of Physics and Astronomy and the Leeds Institute for Biomedical and Clinical Sciences at the University of Leeds, and who led the work. "Chemo- or radiotherapy is often given following surgery to prevent this, but these treatments cause serious side effects." The researchers say that a new technique to control the length of nanotubes underpins the research. By controlling the length, the researchers were able to produce gold nanotubes with the right dimensions to absorb near-infrared (NIR) light-a wavelength for which human tissue is transparent. "When the gold nanotubes travel through the body, if light of the right frequency is shone on them, they absorb the light," explains Professor Steve Evans from the School of Physics and Astronomy at the University of Leeds, who was the study's corresponding author. "This light energy is converted to heat, rather like the warmth generated by the Sun on skin. Using a pulsed laser beam, we were able to rapidly raise the temperature in the vicinity of the nanotubes so that it was high enough to destroy cancer cells." In cell-based studies, by adjusting the brightness of the laser pulse, the researchers say they were able to control whether the gold nanotubes were in cancer-destruction mode, or ready to image tumors. To see the gold nanotubes in the body, the researchers used an imaging technique called multispectral optoacoustic tomography (MSOT) to detect the gold nanotubes in mice, in which gold nanotubes had been injected intravenously. It is reportedly the first biomedical application of gold nanotubes within a living organism. It was also shown that gold nanotubes were excreted from the body and therefore are unlikely to cause problems in terms of toxicity, an important consideration when developing nanoparticles for clinical use.
http://www.bioopticsworld.com/articles/2015/02/multispectral-imaging-method-gold-nanotubes-destroy-cancer-cells.html?cmpid=EnlBowAugust52015&eid=288603243&bid=1143132
|
|
Using a computer model to explore how water molecules connect and nucleate into ice crystals, the researchers found that two types of ice compete for dominance during nucleation: cubic ice (blue) which is less stable, and hexagonal ice (red), which is stable and forms the majority of ice on Earth. Nucleation occurs when water molecules come together to form blobs (pictured above), which grow over time (left to right). Eventually hexagonal ice wins out (not shown). The researchers found that adding new cubic features onto an existing crystalline blob gives rise to nuclei that are more spherical, and hence more stable. In contrast, adding hexagonal features tends to give rise to chains of hexagonal cages that make the nucleus less spherical, and hence less stable. Image: Amir Haji-Akbari, Princeton Univ. |
Researchers at Princeton Univ. have, for the first time, directly calculated the rate at which water crystallizes into ice in a realistic computer model of water molecules. The simulations, which were carried out on supercomputers, provide insight into the mechanism by which water transitions from a liquid to a crystalline solid.
Understanding ice formation adds to our knowledge of how cold temperatures affect both living and non-living systems, including how living cells respond to cold and how ice forms in clouds at high altitudes. A more precise knowledge of the initial steps of freezing could eventually help improve weather forecasts and climate models, as well as inform the development of better materials for seeding clouds to increase rainfall.
The researchers looked at the process by which, as the temperature drops, water molecules begin to cling to each other to form a blob of solid ice within the surrounding liquid. These blobs tend to disappear quickly after their formation. Occasionally, a large enough blob, known as a critical nucleus, emerges and is stable enough to grow rather than to melt. The process of forming such a critical nucleus is known as nucleation.
To study nucleation, the researchers used a computerized model of water that mimics the two atoms of hydrogen and one atom of oxygen found in real water. Through the computer simulations, the researchers calculated the average amount of time it takes for the first critical nucleus to form at a temperature of about 230 K or -43 C, which is representative of conditions in high-altitude clouds.
They found that, for a cubic meter of pure water, the amount of time it takes for a critical nucleus to form is about one-millionth of a second. The study, conducted by Amir Haji-Akbari, a postdoctoral research associate, and Pablo Debenedetti, a professor of chemical and biological engineering, was published online in the Proceedings of the National Academy of Sciences.
"The main significance of this work is to show that it is possible to calculate the nucleation rate for relatively accurate models of water," said Haji-Akbari.
http://www.rdmag.com/news/2015/08/study-calculates-speed-ice-formation?et_cid=4712534&et_rid=614174443&type=cta
|
|
This is an ultra-soft elastomer fabricated by crosslinking bottlebrush polymers contains only crosslinks (red chains) and no entanglements. Courtesy of Li-Heng Cai, Harvard SEAS |
Medical implants mimic the softness of human tissue by mixing liquids such oil with long silicone polymers to create a squishy, wet gel. While implants have improved dramatically over the years, there is still a chance of the liquid leaking, which can be painful and sometimes dangerous.
Now, led by David A. Weitz, Mallinckrodt Professor of Physics and Applied Physics at Harvard John A. Paulson School of Engineering and Applied Sciences (SEAS) and associate faculty member at the Wyss Institute for Biologically Inspired Engineering at Harvard, a team of polymer physicists and chemists has developed a way to create an ultra-soft dry silicone rubber. This new rubber features tunable softness to match a variety of biological tissues, opening new opportunities in biomedical research and engineering.
The material is featured on the cover of the journal Advanced Materials.
"Conventional elastomers are intrinsically stiff because of how they are made," said lead author Li-Heng Cai, a postdoctoral fellow at SEAS. "The network strands are very long and are entangled, similar to a bunch of Christmas lights, in which the cords are entangled and form knots. These fixed entanglements set up an intrinsic lower limit for the softness of conventional elastomers."
http://www.rdmag.com/news/2015/08/eliminating-entanglements-new-strategy-towards-ultra-soft-yet-dry-rubber?et_cid=4731054&et_rid=614174443&type=cta
|
|
After a decade's work a team led by Stanford bioengineer Christina Smolke succeeded in finding more than 20 genes from five different organisms and engineering them into the genome of baker's yeast. In so doing they created two different microbial assembly lines, each of which took less than five days to convert sugar into one of two medicinal compounds: either thebaine, which can be refined into painkillers, or hydrocodone which is a prescription painkiller. The circles on the left represent organisms that contributed genes to the bioengineered yeast. From the top: California poppy, rat, goldthread, bacteria, and opium poppy. Credit: Stephanie Galanie, Smolke Lab Read more at: http://phys.org/news/2015-08-team-genetically-yeast-opioids.html#jCp |
For thousands of years, people have used yeast to ferment wine, brew beer and leaven bread.
Now researchers at Stanford have genetically engineered yeast to make painkilling medicines, a breakthrough that heralds a faster and potentially less expensive way to produce many different types of plant-based medicines.
Writing today in Science, the Stanford engineers describe how they reprogrammed the genetic machinery of baker's yeast so that these fast-growing cells could convert sugar into hydrocodone in just three to five days.
Hydrocodone and its chemical relatives such as morphine and oxycodone are opioids, members of a family of painkilling drugs sourced from the opium poppy. It can take more than a year to produce a batch of medicine, starting from the farms in Australia, Europe and elsewhere that are licensed to grow opium poppies. Plant material must then be harvested, processed and shipped to pharmaceutical factories in the United States, where the active drug molecules are extracted and refined into medicines.
"When we started work a decade ago, many experts thought it would be impossible to engineer yeast to replace the entire farm-to-factory process," said senior author Christina Smolke, an associate professor of bioengineering at Stanford.
Now, though the output is small - it would take 4,400 gallons of bioengineered yeast to produce a single dose of pain relief - the experiment proves that bioengineered yeast can make complex plant-based medicines.
"This is only the beginning," Smolke said. "The techniques we developed and demonstrate for opioid pain relievers can be adapted to produce many plant-derived compounds to fight cancers, infectious diseases and chronic conditions such as high blood pressure and arthritis."
Read more at:
http://phys.org/news/2015-08-team-genetically-yeast-opioids.html#jCp
|
Stanford team members, from the left are: postdoctoral researcher Isis Trenchard, associate professor of bioengineering Christina Smolke, chemistry graduate student Stephanie Galanie and research associate Kate Thodey. Credit: Rod Searcey |
http://phys.org/news/2015-08-team-genetically-yeast-opioids.html
|
|
Dankovich pours contaminated pond water into a funnel containing an antimicrobial filter paper to obtain clean drinking water in a rural area of Bangladesh. Credit: Ali Wilson |
Human consumption of bacterially contaminated water causes millions of deaths each year throughout the world-primarily among children. While studying the material properties of paper as a graduate student, Theresa Dankovich, Ph.D., discovered and developed an inexpensive, simple and easily transportable nanotechnology-based method to purify drinking water. She calls it The Drinkable Book, and each page is impregnated with bacteria-killing metal nanoparticles.
Dankovich will explain her technology and reveal new results of recent field tests conducted in Africa and Bangladesh at the 250th National Meeting & Exposition of the American Chemical Society (ACS).
Although silver and similar metals have been known for centuries to have the ability to kill bacteria, no one had put them into paper to purify
drinking water, Dankovich notes. While earning her doctorate at McGill University, she found that sheets of thick filter paper embedded with
silver nanoparticles could do just that, eliminating a wide variety of microorganisms, including bacteria and some viruses.
She continued her research at the University of Virginia's Center for Global Health, expanding the repertoire of embedded nanoparticles to include ones made of inexpensive copper. Dankovich also began field investigations of water purification applications in Limpopo, South Africa, as well as northern Ghana, Haiti and Kenya.
"In Africa, we wanted to see if the filters would work on 'real water,' not water purposely contaminated in the lab," she says. "One day, while we were filtering lightly contaminated water from an irrigation canal, nearby workers directed us to a ditch next to an elementary school, where raw sewage had been dumped. We found millions of bacteria; it was a challenging sample.
"But even with highly
contaminated water sources like that one, we can achieve 99.9 percent purity with our silver- and copper-nanoparticle paper, bringing bacteria levels comparable to those of U.S. drinking water," Dankovich adds. "Some silver and copper will leach from the nanoparticle-coated paper, but the amount lost into the water is within minimal values and well below Environmental Protection Agency and World Health Organization drinking water limits for metals."
|
If you used any instruments in the Materials Science Center, Soft Materials Laboratory, or the Wisconsin Center for Applied Microelectronics, please remember to acknowledge MRSEC funded instruments and facilities in any publications (DMR-1121288). This will serve as a metric for how often MRSEC funded instruments are used and will help continue MRSEC support in future years. Thanks! If you have any questions, please contact
Felix Lu
.
|
|
|
The Soft Materials Lab
The Soft Materials Lab, housed in the basement of Engineering Hall, has a wide spectrum of instruments for characterizing soft materials. The lab is managed by
Anna Kiyanova who is available to answer all of your characterization questions. Some of the instrumentation in the SML is listed below:
Gel Permeation Chromatography (GPC)
Dynamic Scanning Calorimetry (DSC)
Thermo-Gravimetric Analyzer (TGA)
Dynamical Mechanical Analyzer (DMA)
Rheometer
FTIR, PM-IRRAS, Fast Mapping Raman, Spin coater, Environmental SEM, Filmetrics F20 Reflectometer, Oxygen Plasma Asher, Contact Angle imager, atmospheric & vacuum ovens
Contact: Anna Kiyanova [email protected] (608) 263-1735
|
The Materials Science Center (MSC)
The Materials Science Center has a wide spectrum of electron, optical and physical charaterization instruments, some of which are listed below. The MSC is fully staffed with highly experienced instrument expertise to help you with your sample characterization and data interpretation.
FE-SEMS with EDS
(S)TEMs with EDS/EELS & Cryo Capable
Atom Probe
XPS with Cluster Gun
AFM/BioAFM
Laser Scanning Confocal Microscope
Raman Microscope with multiple excitation sources
FTIR
ZYGO optical Profilometer
Fluorimeter
Tabletop SEM
UV-VIS spectrometer
Nano-Indenter
FIB
Sample Preparation facilities
sputter coaters/ion mills
XRDs
Contact: Dr. Jerry Hunter [email protected] (608) 263-1073
|
The WCAM is a full spectrum micro/nano fabrication facility for processing and integrating devices in Silicon, III-V, group four, glass, plastic, materials. On site, fully-qualified and highly experienced staff are available to help you with your process development and answer questions. Processing capabilities include:
Photo/nanoimprint Lithography
wet/dry etching
metal /dielectric deposition
dielectric film growth
MEMS processing (critical point drying, wafer bonding and alignment, etc.)
packaging (wire bonding, die attach, dicing, curing)
Contact: Dan Christensen [email protected] (608) 262-6877
|
Wisconsin GEO-Science materials characterization facility
The materials characterization facility in the Geology dept has some complementary instrumentation along with materials experts to help you with your charaterization and sample prep challenges! A partial list of instruments is listed below:
Electron Microprobe Analysis SEM XRD (with Cobalt source) SIMS Lab
and many more!
Contact: Dr. John Fournelle Dept of Geology & Geophysics University of Wisconsin-Madison 1215 W. Dayton St Madison, WI 53706 (608) 262-7964 (office) 265-4798 (lab) 262-0693 (fax) johnf*at*geology.wisc.edu
|
Explore the Geology Museum and take a peek into Wisconsin's
deep history! On your visit yo
u can touch rocks from a time when there were volcanoes in Wisconsin; see corals, jellyfish and other sea creatures that used to live and swim where we now walk; and stand under the tusks of a mastodon while imagining yourself in the Ice Age. Also on display at the Geology Museum are rocks and minerals that glow, a model of a Wisconsin cave, dinosaurs and meteorites. Our mineral, rock and fossil collections have the power to educate and inspire visitors of all ages. Come see for yourself!
|
Science Cafes
What is a science café?
Science cafés are live grassroots events held in casual settings like coffeehouses and pubs that are open to everyone, organized locally and feature an engaging conversation with a scientist on a particular topic. Science cafés have been held in communities across the globe for years. To learn more, visit sciencecafes.org
Who should attend?
Everyone! S
cience cafés are free and open to the public.
No prior scientific knowledge is needed, so anybody can participate.
What would I do at a science café?
Science cafés start with a presentation by a scientist or group of scientists about the evening's topic. Then the conversation about the topic begins.
A science café is not a formal lecture-audience members are encouraged to ask questions and participate in the discussion.
|
Student tour groups of your facility
|
Industrial facilities tours?
Are you interested in showing off your facility to interested student groups? Do you want to increase exposure of what your company does to encourage higher application rates and get student interns? Hosting a tour might be a good start! Please contact
Felix Lu or
Erin Gill to initiate this!
|
Using our campus facilities
|
The Practical Side of Things
|
One of the more common manufacturing methods has technicians making structured 3D semiconductors by first growing a crystal, then slicing and polishing it into a thin wafer, known as the substrate. Layers of crystals are grown on the substrate's surface and shot with ions to fill gaps in the 3D matrix of the semiconductor. This creates the p- and n-regions.
It has proven more cost-effective from a fabrication standpoint, since thousands of LEDs are made on a single wafer. For example, a 2-in. diameter wafer can yield up to 6,000 LEDs. However, producing a single LED chip from a wafer requires a specialized cutting process, which inevitably reduces the overall yield. Thus, to lower the price of LEDs and semiconductors, a better method is needed to separate them.
Read more!
http://machinedesign.com/embedded/abcs-leds
|
Soldering, brazing, and welding are all methods of joining two or more pieces of metal and selected other materials. They are also methods used to fill gaps in metal parts.
In welding, the two metals (or thermoplastic) must be similar. For example, copper cannot be welded to steel. Welding uses high temperatures to melt and join two metal parts. A filler metal is often used as well. When properly done, the finished weld is as strong as the surrounding metal. But if the process is not carried out and the welder applies too much heat, it can change the metal's properties and weaken the weld. There are several different types of welding, including metal inert gas (MIG), arc, electron beam, laser, and stir friction. Welding is also widely used to slice apart large metal structures by melting through them.
Read more!
http://machinedesign.com/fasteners/whats-difference-between-soldering-brazing-and-welding
|
Tapping screws form mating threads in materials they are driven into. There are two basic types: thread forming and thread cutting.
The thread-forming screw displaced material around the pilot hole so that it flows around the screw's threads. These screws generally are used when large stresses are needed to increase resistance to loosening. Because no material is removed, the mating part creates a fit with zero clearance. They usually do not need lockwashers or other types of locking devices to prevent loosening.
Thread-tapping screws have cutting edges and chip cavities that create a mating thread by removing material from the part they are driven into. The screws' cutting action means torque needed for insertion is low. The screws are used in materials where disruptive internal stresses are not wanted, or when it takes to too much driving torque to use thread-forming screws.
Read more!
http://machinedesign.com/fasteners/whats-difference-between-thread-forming-and-thread-cutting-tapping-screws
|
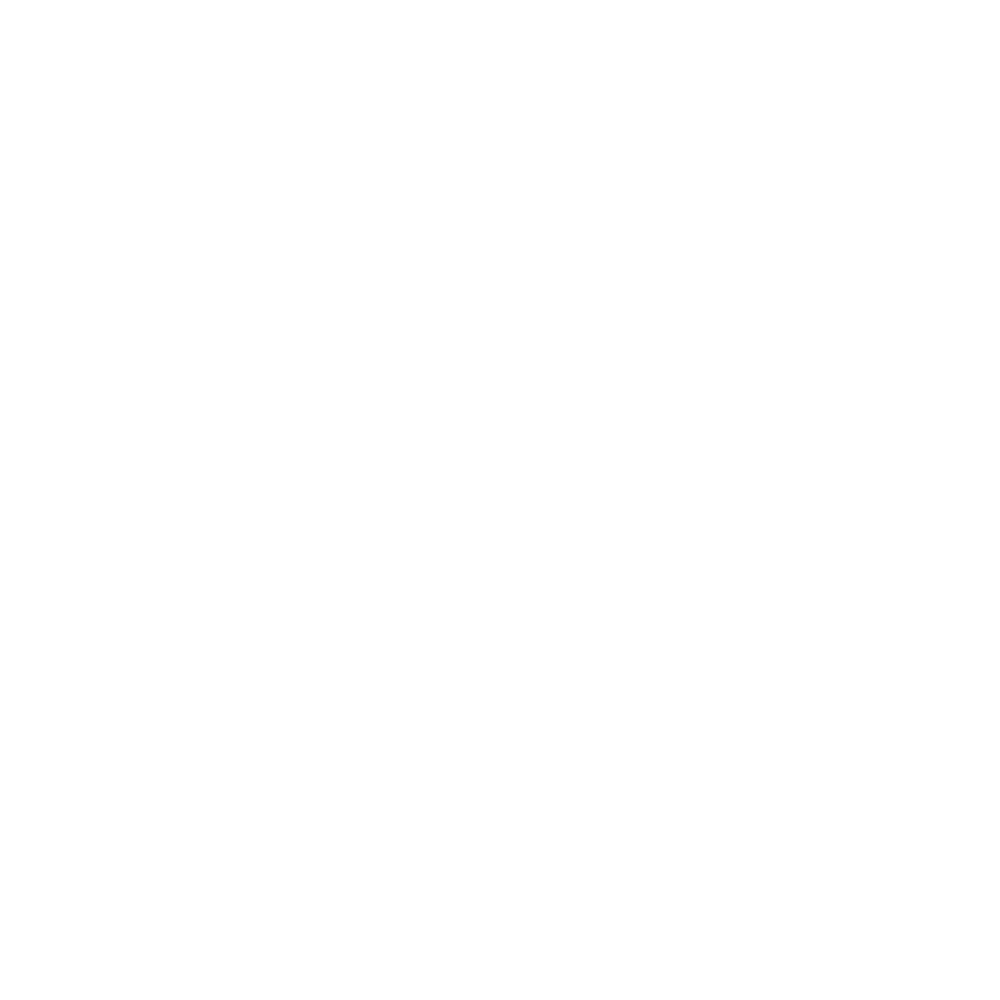 |
|
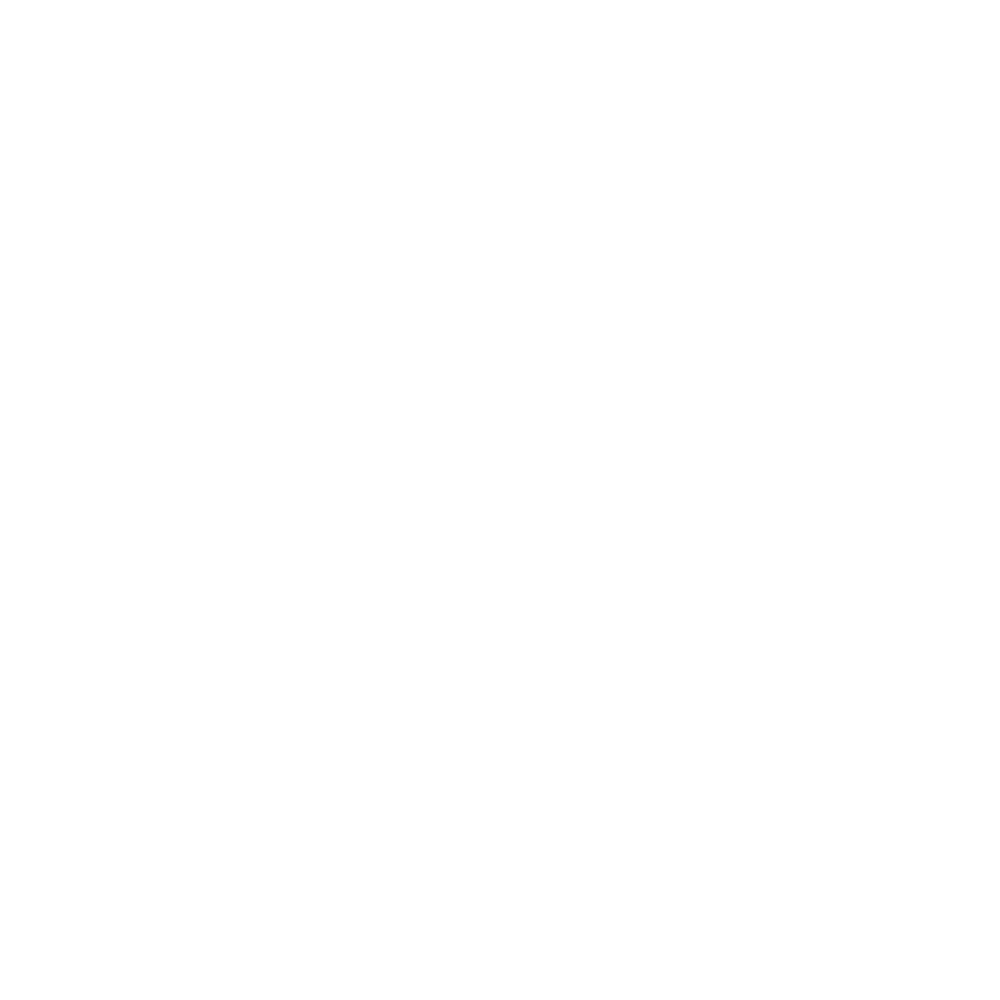 |
|