Information for our Residential Building Community
FOCUS: Meter Box Setup and Common Failures
|
|
Our goal at Austin Water is to assist you with a successful residential water meter installation on the first attempt. The Taps Office will issue bi-monthly newsletters with focus on a particular aspect of residential water. The previous newsletter (
AW Taps Newsletter Sept 2017, release 09/25/2017
) addressed:
- Water Meter Inspection Request Process
- Meter Installation Timeframes
- Common Meter Inspection Failures: Meter Box Cleanliness/Accessibility, Spacer, Double-Meter Box Issues
- Water Meter Inspection Checklist
This newsletter expands on proper meter box setup for a new water meter as well as common inspection failures that require re-inspections.
|
|
These pictures illustrate acceptable meter box installations that allow Austin Water to complete a water meter installation. Note the neatness of the installations, the proper spacing, and configuration of the plumbing connections.
|
|
Correct meter box setup as outlined on Standard Detail 520-AW-02. NOTE: current standard requires use of a wooden dowel instead of vented PVC spacer.
|
|
Figure 1: Meter box to grade with no obstructions
.
|
|
Figure 2: Double meter box with properly spaced connections using wooden dowels.
|
|
- Meter box and lid: COA-approved version must be set up for correct meter size, installed to final grade, and free from defects, large cut outs, and damage. At the time of inspection, the meter box must be accessible, clean and free of debris and construction spoils.
- Lead-free parts: both the 1-1/4” x 3/4” reducing bushing and the 8-1/2”x 3/4” meter nipple must be made of lead-free materials.
- Wooden dowel (previous, vented meter spacer): installed and clearly marked with service address. This avoids tampering concerns (fines imposed) as well as clarifies premise address plumbing lines for double-meter boxes.
- Customer cut-off valve box is to be set up in accordance with Standard Detail 520-AW-02 using items contained within the Current Standards Products List including COA-approved meter box and COA-approved ball valve.
- Customer cut-off valve box and lid: COA-approved version must be set up for correct meter size, installed to final grade, and free from defects, large cut outs, and damage.
- Ball valve: stainless steel with wing type handle.
|
|
Scheduling the Meter Inspection
|
|
- Do not request the inspection until the site is ready. If the inspection fails, a request for re-inspection will be required which may take up to an additional ten (10) business days and may be assessed a fee.
- Ensure Austin Water received an acceptance letter stating the development is complete.
- Ensure Austin Water received a meter release verification form from a Development Services Inspector stating the water meter may be installed.
- Ensure the plumbing inspector approved your private yard line.
- Ensure any development corrections cited by Austin Water Engineering were cleared and the Taps Office was notified.
- Ensure any re-inspection fees have been paid. Outstanding balances are to be paid via the City Cashier (512-972-0009 / M-F 8:00AM-4:00PM, closed from 12:00PM-1:00PM). Have your invoice number available when you contact the Cashier to make a payment.
|
|
In the event of a failed inspection, a Meter Service Investigator will leave a Correction Notice containing a brief summary explaining the reason for the failure. Examples:
- Meter box not set up for correct meter size.
- Meter box position incorrect/not set to grade.
- Meter nipple, yard line, angle stop not properly aligned.
- Damaged meter box.
- Angle stop high/low and needs adjustment.
- Unvented meter spacer identified (tampering fees to be assessed).
- Corrections previously identified not corrected.
- Engineering Violation (must call 512-972-3514). EX: meter in driveway/sidewalk.
- Additional corrections necessary.
|
|
Common Inspection Failures
|
|
Our meter investigators are unable to provide on-site training to resolve inspection issues. Prior to requesting a meter inspection through the IVR phone scheduling, please ensure the site is fully prepared with private yard plumbing, meter box/required parts, and customer cut-off valve box/required parts are installed according to standards, and the site is ready for immediate inspection without potential for delays. Typical failures may result in re-inspection fees. The most common failures are described below.
|
|
Meter box set up: (1) box, parts and/or plumbing lines not set up for correct meter size; (2) meter nipple, yard line, angle stop not properly aligned; (3) angle stop high/low and needs adjustment.
|
|
Meter box position incorrect/not set to grade.
|
|
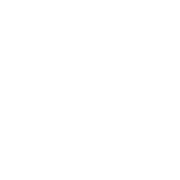 |
Figure 1: Plumbing lines not properly aligned. Affects meter box placement.
|
|
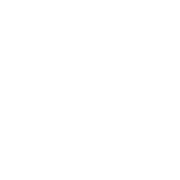 |
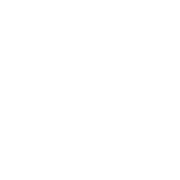 |
Figure 2: Meter box and shutoff valve boxes not to grade.
|
|
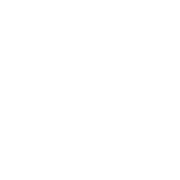 |
|
Incorrect parts: lead-free parts not yet replaced, required parts missing, or incorrect part sizes for assigned meter size.
|
|
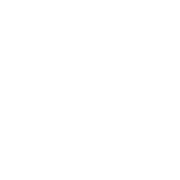 |
Figure 1: Meter box not set up per specifications and is missing parts.
|
|
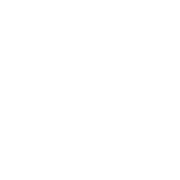 |
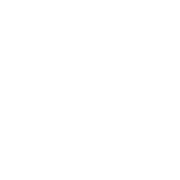 |
Figure 2: Correctly installed meter box with required components.
|
|
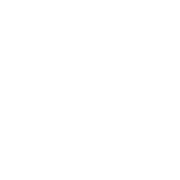 |
|
Meter box damaged or cut; non-COA meter box used, meter box not preset, or not set for correct meter size.
|
|
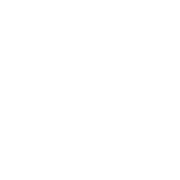 |
Figure 1: Non-COA meter box used.
|
|
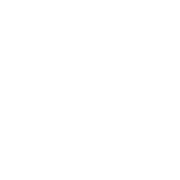 |
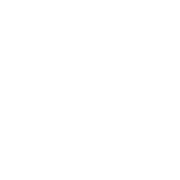 |
Figure 2: Correctly installed COA meter box with no obstructions or damage.
|
|
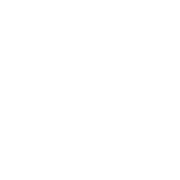 |
|
Double meter box: wooden meter dowel not labeled for correct address.
|
|
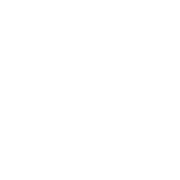 |
Figure 1: Missing dowel spacers and premise addressing.
|
|
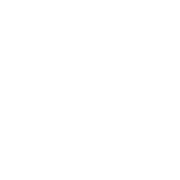 |
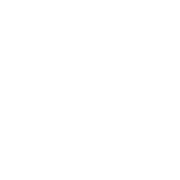 |
Figure 2: Wooden dowel correctly installed with premise address shown.
|
|
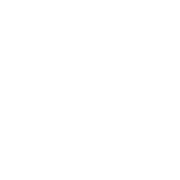 |
|
Inaccessible meter box: interior contents flooded, covered by construction materials/spoils, blocked by vehicle, or incorrectly placed in private fenced yard.
|
|
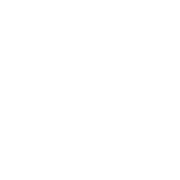 |
Figure 1: Meter box incorrectly installed in private fenced yard.
|
|
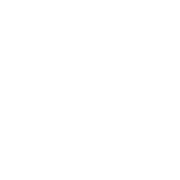 |
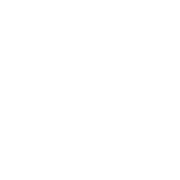 |
Figure 2: Meter box buried and full of mud.
|
|
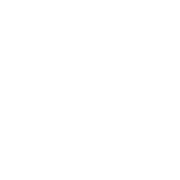 |
|
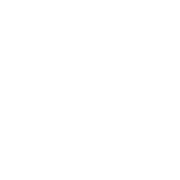 |
Figure 3: Meter box could not be located.
|
|
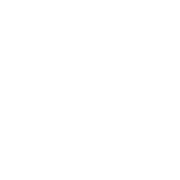 |
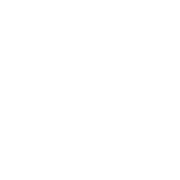 |
Figure 4: Meter box flooded.
|
|
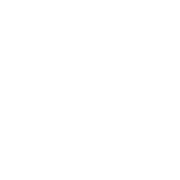 |
|
Unvented spacer (tampering issue) in lieu of wooden dowel with spacer installed at incorrect length or misaligned (placed at an angle).
|
|
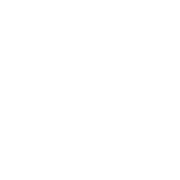 |
Figure 1: Misaligned spacer.
|
|
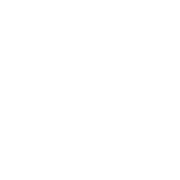 |
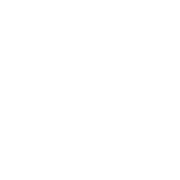 |
Figure 2: Non-vented spacer used instead of wooden dowel. Tampering issue, thus lock was installed.
|
|
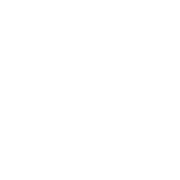 |
|
Corrections previously identified not corrected.
|
|
Engineering violation (512-972-3514): meter set in driveway, sidewalk, near electrical box.
|
|
Figure 1: Irrigation cutoff install before customer cutoff.
|
|
Figure 2: Meter box placed in driveway.
|
|
Figure 3: Meter box set near electrical.
|
|
Water Meter Inspection Checklist
|
|
3. Is the meter box in good shape—free from defects, large cut outs, and damage?
4. Has the meter box been set up for the correct meter size?
5. Is the COA-approved meter nipple installed?
7. Is the property owner’s valve box installed to final grade?
8. Are all parts free from defects in workmanship or materials?
9. Is the meter box free of debris, mud, construction spoils?
10. Is a wooden dowel installed and clearly marked with the service address?
|
|
|
|
|
|
|