The City of Frankfort, Kentucky serves more than 27,000 people and processes over 7 million gallons of sewage per day. Over 235 miles of sewer lines and 48 pump stations transport the waste to the plant. When it rains, the city has a combined sewer overflow system and a wet weather detention facility for excess flow. Pump stations can be overwhelmed after a heavy rainfall because of hilly terrain. Detailed information and reliable monitoring of each pump station are essential to intercept problems following heavy rain.
|
Downtown Frankfort, Kentucky. Source: Wikipedia |
Frankfort Collection Systems deputy director Bob Peterson says Mission system data provides the detail they need to react quickly to overflows. Before 2003, the treatment plant and 25 pump stations were fitted with autodialers that took up to15 minutes to report status information.
"The autodialers would call us and give us an update but that's really all it was doing for us," Peterson explained. "We were looking for something that was much more reliable and provided the information in real-time."
Peterson's first project was to replace the outdated monitoring system. Management evaluated a traditional remote SCADA system with private radios as well as a satellite-based system. Those options were too expensive and did not provide what the city needed.
"Nextel was our cell phone provider at the time. Representatives introduced us to Mission and that is how we learned of the system nearly a decade ago," explained Peterson.
|
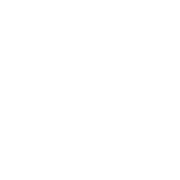 |
Bob Peterson stands next to one of the city's 55 pump stations. Photo Credit: Bob Peterson |
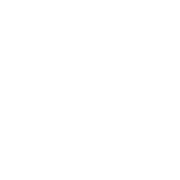 |
Peterson says he initially thought a telemetry system replacement could take several years. The original budget for hardware and startup on 55 stations was $875,000. Mission RTUs were installed on all stations in operation at the time for less than $200,000.
"The Mission system has been working very, very well," Peterson explains. "The guys that work with the pumps were not too excited about it because they thought it was going to track their work progress. Now they use it as a tool. Our electrician studies the system. When there is a problem with a pump he refers to the Mission system to determine what is happening."
Pump data helps the electrician remotely diagnose a pump station issue and come prepared to the site with the tools needed to fix the problem.
"Having more data has saved us from making two trips every time something is malfunctioning," Peterson explains.
Pump runtime and start reports are used to determine if pumps are short-cycling or running longer than normal. Personnel compare flow and pump runtimes to verify the numbers are optimal at each station. Team members use the desktop and mobile interfaces to view the Mission portal and have tablets in the field to view data when visiting a station. Rainfall data is used to study inflow and infiltration issues. This is especially important when a rainfall follows a dry spell. Runtime variance reports help staff pinpoint major fluctuations.
"We use the data quite extensively to identify where our worst problems are," Peterson explains. "It helps us to schedule and prioritize our improvement projects, whether it's rebuilding a pump station or doing an inflow and infiltration reduction project."
The Mission system successfully notifies Peterson of excessive pump starts so they can be fixed before there is a failure. Prior to Mission, staff members only knew there was a pump problem if someone found it during a routine station visit. The system has also saved on power bills.
"The Mission system has also helped us with power usage discrepancies with the power company," Peterson explains. "They used to tell us that we must have been having problems with the pumps. We are able to monitor the power and go back to the power company with data that shows how the power is fluctuating. That has saved us money from a power usage standpoint."
|