-
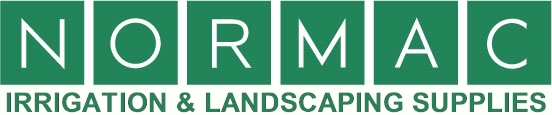
-
|
|
|
Professional Contractors Update
|
July 2019
|
|
|
Aging and inefficient irrigation systems are a big profit opportunity for your company.
Irrigation systems that are more than 10 years old begin to experience declining efficiency and increasing repairs from aging equipment.
Get into the spirit of Smart Irrigation Month in July by supporting efficiency upgrades.
How can you convince current customers to buy upgrades? On service visits, technicians should follow the observe, recommend, sell process:
Observe: Look beyond trying to find "what is currently broken" to identify repairs and upgrades that are needed because equipment is worn or not up to the latest efficiency standards.
Recommend: Connect with the customer and provide a checklist of issues that need to be addressed. Use sales tip sheets to educate the client. Have sheets on common topics like nozzle upgrades, smart controllers, sprinkler-to-drip conversions, etc.
Sell: Be sure technicians can quote a price for needed upgrades to the customer on the spot. Carry the correct inventory on trucks so the work can be completed during the call rather than scheduling a second visit.
Develop the healthy habit of driving more upgrade sales. Your customers and your bottom line will thank you!
|
|
5 Reasons Why You Need to Offer Rain Bird WiFi Controllers to Your Irrigation Customers
Reason 1: Rain Bird's LNK allows you and your customer to program their controller from anywhere, with the convenience of a mobole device.
Reason 2:
Rain Bird's LNK WiFi Module gives real-time alerts and advanced water management tools. This gives you alerts that can lead to profitable service work.
Built-in mobile notifications provide troubleshooting access, simplify service calls, and warn of freezing conditions when expected.
Reason 3: When you're on-site, your phone acts like a wireless remote control for an irrigation system. No separate hand-held remote required - and no distance issues either.
Reason 4: Rain Bird offers a professional app that allows for simple multi-site management and as well as remote diagnostics.
Reason 5: Help your clients enjoy the benefits of automatic water updates like a true smart controller. Automatic weather adjustments provide daily run time changes, saving up to 50% in water.
|
Why is it so important to have a well-stocked and organized service truck? The key reason is productivity. A
service technician who has no problem finding parts, supplies and tools can get right to the task at hand.
Plus, customers are always happy to hear "I've got the part right here on my
truck and can fix that right away." A stocked
truck also saves unnecessary and time-consuming stops to pick-up miscellaneous supplies.
For our customers' convenience, we offer a complete line of
Christy's tools and job site essentials to make stocking and re-stocking your
trucks easy. Just shop the convenient displays in our stores to grab the items you need to ensure that you always have the right consumable supplies to
get jobs done quickly, correctly and safely.
Click here for a printable checklist to guide you in selecting and stocking job site essentials for spring irrigation
service. Provide a copy to each of your technicians to be sure each of your
trucks is stocked and ready.
|
Kichler's new 12V integrated LED accent light has the durability you expect with a modern look, strong performance and superior light quality.
This fully sealed and encapsulated fixture keep all critical components protected against the elements, including a 4,000-volt surge protection guards against power irregularities that can be a hazard to LED landscape lighting.
Kichler's custom T.I.R. (Total Internal Reflection) acrylic optics assure no halos or scallops - just superb, center-to-edge uniformity for clean, clear light. The LED product is available in spot light, flood light and wide flood light beam options putting light exactly where you need it.
Take your projects to the next level with the new 12V LED Accent Light and Kichler as your trusted partner.
|
NDS Professional Irrigation products save time, money and water!
With a features a low opening pressure of 7.5 PSI NDS Dura Flo CV features 15% longer run lengths than the other leading brands.
No Root Intrusion.
The combination of check valve and anti-siphon capabilities protects each emitter from clogging and root intrusion. No Copper or Treflan required.
An efficient emitter design that provides pressure compensation, check valve and anti-siphon protection, makes Dura Flo CV the perfect solution for all low volume applications.
Combined with Smart Loc™ fittings, Dura Flo CV™ is faster and easier to install, check out our installation videos to see for yourself!
The new and improved Smart Loc fittings feature flanges that make it easier to install and reusable. They are a universal fit for all supply and drip line brands.
The Universal Pop up Conversion Kit with Cap Off. This industry first allows contractors to quickly convert any pop up sprayhead to a fully functional drip system. Using our patented bi-directional Y-filter regulator, the conversion kit installs at grade for a clean finish.
|
Tips for Solvent Welding in Hot Weather
There are many occasions when solvent welding plastic pipe in 95°F temperature and above cannot be avoided. However, by using Weld-On solvent cements and by following the standard instructions with a little extra care as outlined below, successful leak-proof joints can be made in even the most extreme hot weather conditions.
Here are some tips to follow when solvent welding in hot weather:
1. Store solvent cements and primers in a cool or shaded area prior to use.
2. If possible, store pipe and fittings, or at least the ends to be solvent welded, in a shady area before solvent welding.
3. Cool surfaces to be joined by wiping with a damp rag. Be sure that the surface is dry prior to applying the solvent cement.
4. Try solvent welding the joints during the cooler morning hours.
5. Make sure that both surfaces to be joined are still wet with the solvent cement when putting them together. With larger size pipe, more people on the crew may be necessary.
6. Using a primer and heavier, high viscosity solvent cement will provide a little more working time. Vigorously shake or stir the solvent cement before use.
7. There can be a greater expansion-contraction factor affecting the pipe in hot weather. We suggest you follow the advice of the pipe manufacturer regarding this condition. Anchored and final connections should be made during the cooler hours of the day.
|
Offering Mid-Season Irrigation Audits to Your Customers
Are you offering mid-season check-ups to your irrigation customers?
They're certainly a big opportunity! Many customers do not notice when they're system has broken components or is running inefficiently. This leads to wasted water and stressed landscapes.
During a typical check-up,
the sprinkler expert can perform
regular maintenance and help customers avoid unexpected summer service calls. Essential tasks include:
Setting an Optimal Summer Watering Schedule - the correct controller program will tame your customers' water bills by watering precisely when needed.
Check Operation and Adjust Sprinklers - making sure they're directed onto landscaped areas and not spraying the house, walkways or driveway.
Check for Broken Risers and Leaks - a leak no larger than a tip of a ballpoint pen can waste 6,000 gallons of water a month.
Correct Coverage Problems - caused by
broken nozzles, interference from plants or other
issues. In systems with poor
coverage, you have to overwater some areas just to get other areas to stay alive. By resolving
coverage
problems, there's no need for overwatering.
Don't wait... with the hottest, driest months ahead. Your customers need a mid-season tune-up now.
|
|
|
|
|
|
|