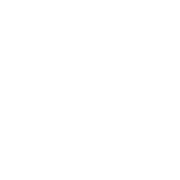 |
The European Space Agency (ESA) builds spacecraft such as space probes, rovers and satellites for scientific research, technology demonstrations and operational services.
|
ESA currently has, or has had, spacecraft in orbit around all the planets in our solar system, as well as a fleet of research and operational satellites in various orbits around the Earth. Even a major part of NASA's new spacecraft for the Artemis moon program is built by ESA.
The planning, assembly and testing of ESA's spacecraft is either followed or done at ESA's technical centre ESTEC in Noordwijk in the Netherlands.
Here some of the largest clean rooms and specialized test chambers in Europe are located: for example the LSS (Large Space Simulator), Europe's largest vacuum chamber, to test the thermal integrity of spacecraft, as well as HYDRA, the largest European shaker table, to ensure that spacecraft can handle the intense vibrations during launch.
|
Saving time and money in simulation and testing
|
The design, assembly and test phases of a spacecraft's development process must be thoroughly documented and archived, for later reference and mission control, as well as for future versions of the spacecraft.
However, building and testing a spacecraft generates a high amount of data, often from multiple sources, in various versions, and in different electronic formats. This data must all be compatible and accessible with each other to prevent cumbersome and time-consuming processes.
DEFINE (Multidisciplinary 3D Digital models for AIT environment), Jotne's new project for ESA, will deploy a standardized format for digital models and simulation data for spacecraft development. The DEFINE project will utilize ISO 10303 (STEP) and more specifically its application protocol AP 209:Application protocol: Multidisciplinary analysis and design. This will improve the efficiency of the spacecraft assembly, integration and test procedures.
|
- "One of the challenges in the DEFINE project is the large number of different simulation and 3D tools that are in use, with no standard for making them mutually compatible and accessible, The response to this is to use open, international and public available standards" - says Kjell Bengtsson, VP at Jotne.
These models often contain different kinds of information at different levels of detail. Thus, defining an electronic format capable iof maintaining the "as tested" configuration of the spacecraft, from computer simulations at the planning stage, through assembly of the spacecraft, to the pre-flight testing at ESTEC, will be crucial.
Some of the tools to be integrated into DEFINE are: tools for 3D CAD (e.g. Catia, Solidworks, NX...) Thermal and Optical simulations (e.g. Nastran, Lighttool...) and sensors' set-up/test data acquired on the test floor.
The DEFINE project will lead to extensions of the Jotne software EDMopenSimDM available for other users and applications.
The DEFINE project continues until the end of 2021.
|
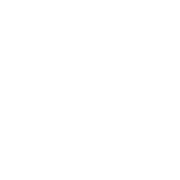 |
|
|
|
|
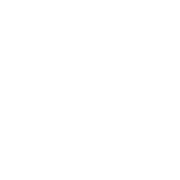 |