FOLLOW US!
All meetings & groups are temporarily cancelled due to COVID-19 protective measures |
UPCOMING CLASSES
We are now holding some classes with a limited number of students. If you attend, you will be asked to wear a mask.
Keep an eye on your email for our
2021 class list!
WEAVING
Nov 14
Dec 4-5
FELTING
Dec 17
Dec 8
Dec 12
Weaving Refresher
by appointment
541-688-1565
|
Eugene Textile Center
Facebook Group
for Creative Customers
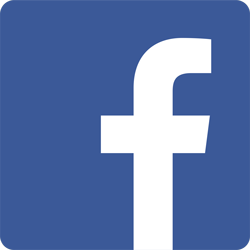 Join the conversation, show off your latest projects, and connect with other ETC customers.
|
Check out the new Weaving Resources section on our website. We will be adding new articles and information, so don't forget to check it out once in a while. Don't worry! We'll be adding spinning, dyeing, and felting resources as well!
|
|
|
We are open regular hours: Mon-Sat, 10am - 5:30pm
|
It's Time to Get Ready for the Holidays!!
There are only SIX weeks left until Christmas (how did that happen??)
We'd like to help you out with
10% OFF almost everything we sell!
Sale lasts until the last day of November
|
Are you ordering something large this holiday season?
Get your loom and wheel orders in ASAP to beat the rush and make sure it gets to you in time.
|
We will be hosting a low-key Holiday Market this year for local creators to sell their amazing products.
Market opens on Nov. 27th, the Friday after Thanksgiving and will last through Dec. 24th
Stop by and support local artists <3
|
Spots are open to anyone (limit of 15 items). Just fill out an inventory sheet and stop by the store to check them in.
|
Fermented, fresh, instant ... there are a lot of different options when using indigo for dye. We sell Instant Indigo granules that make getting started with indigo easy!
To help you get going, Janis has written some simple instructions for your first indigo pot. Check them out on the Dyeing Resources Page!
|
Indigo dye can be prepared from many different plant species found around the world. The oldest example of indigo dyed yarn comes from Peru (no surprise there!) from six thousand years ago! Other early examples are from Egypt (4400 years ago), and China (3000 years ago).
The most prolific producer of indigo dye in the ancient times was India. In fact, the name indigo comes to us from the Greek word indikón which is both their word for Indian and the indigo dye. Blue dye-plants weren't limited to the tropics (where "true indigo" grows). Japanese Indigo grows in more temperate climates (like Oregon!), and Woad is native to the steppes of Asia and has been spread to Europe.
Plants aren't the only source of blue dye. Certain mollusks found in the Mediterranean secrete a substance that contain mixtures of indigo (blue), mono-bromoindigo (purple), and di-bromoindigo (red). The earliest evidence for the use of these mollusks for dye comes from Crete. They developed a method of extracting the dye (it involved smashing, fermenting in an alkaline solution, and cooking for over a week). The Phoenicians later improved on the methods and become famous for their Phoenician Red and Tyrian Purple. If the dyed material is exposed to ultraviolet light while curing, the di-bromoindigo converts to indigo, resulting in a pure blue rather than a purple color. Some scholars believe this is the elusive source of tekhelet, or the blue traditionally found on Jewish religious garments (and represented on the flag of Israel).
|
Free Last Minute Lecture with the Seattle Art Museum
10 am Saturday, Nov 14
Colors of the Earth, Colors of the Sky:
Bingata Textiles of Okinawa
with John Marshall
If you missed out, you can read about Bingata Textiles on John's website
|
Needle Felted Forest Homes
|
New Class!
Tues, Dec 8 or Sat Dec, 12 from 10-4 (bring a lunch!)
We will be making a forest home for a forest gnome. After we create the house base, we will be adding windows, doors, and landscaping.
$60 + $20 for materials
|
In the weaving world, there are many types of looms. We quite often get asked which we think is the best. Answering that question is tricky! Each loom has its own quirks and personality and is best suited for different styles of weaving (or different weavers). Before we dive too deep, there are a few concepts that are common to all looms. Understanding these can help you make sense of their differences.
|
Warp, Weft, & Shed
Every loom provides a frame that helps the weaver stretch the warp out. This can be as minimal as a couple small sticks (as in a backstrap loom) or a large edifice that takes up an entire room. The warp is the length-wise yarn that is attached to the loom. The most simple loom would require the weaver to weave the weft (that's the yarn that goes back and forth) over and under each warp yarn. This method is fairly time consuming and weavers have devised many shortcuts for separating the warp threads so that the weft yarn can be quickly interlaced. The open space between the warp yarns is called 'the shed,' (think of it as looking a bit like the profile of a shed roof). A shed is usually created by a shed stick turned on edge or a series of heddles that the warp threads pass though and let the weaver manipulate groups of warp yarns all at the same time.
|
Types of Sheds
A shed can be created by lifting certain warp threads (called a rising shed), by lowering certain warp threads (called a falling or sinking shed), or by simultaneously raising and lowering warp threads. One of the key differences between looms is the type of shed they create and how they created it.
|
Loom Mechanics, or How to Create a Shed
I'm not going to talk much here about many of the smaller looms like inkle, tapestry, tablets, etc because they are all very specialized ... maybe in another newsletter!
Now on to the nitty-gritty of how sheds are created.
|
Jack Looms
The Jack Loom is the most common type of loom found in the USA. It works by either pushing or pulling a set of shafts (with heddles) in order to raise or, in a small number of looms, lower the warp. A jack works on a pivot that is controlled by the treadles. The treadle pushes down, pulling one side of the jack down, which pushes the other side up, lifting the shaft! Schacht and Gilmore looms are great examples of this style.
|
46" weaving width & comes with bench
|
The Wolf looms are ultra portable and solid. All Schacht looms have the EASIEST tie-up system. Widths range from 18" to 45" with 4-8 shafts.
New looms range from $1,327 to $4,482 after the 10% discount |
The jacks can also be placed above the shafts with a system of pulleys to or rods that move the jacks that lift the shafts. Macomber and Harrisville Designs looms are examples of this style of jack loom.
Not sure of you have a jack loom? Take a look at your shed when you press a treadle. Does part of the shed stay still while the rest moves? Unless you are on a table loom, this is likely a jack loom!
|
Quiet, small, & portable. Fantastic for lightweight projects. Loom waste is super minimal!
New looms range from $2,230 to $2,534 after the 10% discount |
Counterbalance Looms These next two styles of loom share the same shed type and are the ones people most often get confused. The counterbalance loom works with pairs of shafts that are connected to each other. When one shaft goes up, the other must go down. When looking at the shed of a counterbalance loom, some of the threads move up and the rest move down. This is the same SHED as a countermarch, but the mechanics of a countermarch are very different. Counterbalance looms work great for 2/2 twills and plain weave. They start to struggle a bit when asked to weave 3 to 1 or if you add more than 4 shafts. These make wonderful rug looms. |
Countermarch Looms
Countermarch looms are very popular in the Scandinavian countries and most of the new countermarch looms you can buy today are built in Europe.
Countermarch looms work by simultaneously pulling some shafts up and some shafts down. Unlike the counterbalance, each shaft is controlled individually. This means that you can tie up a countermarch loom any way you like and it will still work beautifully. Rather than balancing shafts against each other, countermarch looms have two sets of lamms that lift and lower the shafts. It can sometimes be tricky to tell apart some countermarch looms and a jack loom with upper jacks, but just look at the shed and see if it opens up and down (countermarch loom) rather than only lifting some warp threads (jack loom). You can read more on Glimakra USA's website
|
Quiet, versatile, and built like tanks. These are classic looms that will never go out of style. The overhead beater and countermarch action makes this one of the most ergonomic looms. Easy on the knees & shoulders.
New looms range from $1,575 to $6,120 after the 10% discount |
Rigid Heddle Looms
The rigid heddle loom is in a bit of a special category as you only thread every other warp yarn through a heddle (the other goes through a slot hole) that is ALSO your reed. When you physically pull the shaft/reed up, those half of the warp threads go up. When you push the shaft down, those same threads go down. This creates an interesting effect where your heddle-hole warp threads are doing all the work. As long as you are not weaving with a very stiff material like linen, the yarns work themselves out to remain balanced. In order to get fancy sheds with the rigid heddle loom, you need to use pick up sticks and/or extra shafts/reeds.
Rigid heddle looms really shine for quick weaving (I've seen Liz Gipson dress a loom for a scarf in 18 minutes!), versatile pick up that is more impractical on a floor loom (the pick up stick goes behind the shafts), and extreme portability.
|
30" weaving width & comes with EVERYTHING
|
Table Looms
This is a trick category! Table looms can actually work using any of the previous loom mechanics (counterbalance, jack, etc) and are only truly defined as small looms that can set on a table.
Most popular table looms today work through a direct lift style of design. Each shaft (or sometimes a set of shafts) is directly attached to a lever on the loom. The weaver pulls the lever which in turn pulls a cord attached to the shaft. The Ashford and Louët table looms are examples of this style.
|
Sincerely,
Suzie, Staff and Buddy (the shop puppy)
Eugene Textile Center 2750 Roosevelt Blvd., Eugene, Oregon 541-688-1565
|
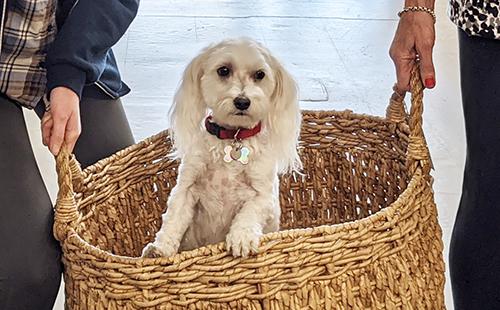
|
|
|
|