(January, 1909, pp. 82-83)
|
Forging and Hardening a
Hand Hammer
James Cran
|
In making a hammer the first thing to do is select a piece of cast steel of at least 0.75 carbon, either round or octagon in section. If the hammer is to be used as a blacksmith's hand hammer material 1 3/4" inches in diameter is sufficiently heavy. The first operation is to flatten enough of the bar to form the eye and the pene. After flattening, draw down the portion for the pene to about 1 1/8" inches in diameter if it is to be ball shaped. If it is to be a cross pene, it should be drawn to about the same dimensions square. When this has been done punch a hole for the eye considerably smaller than it is meant to be when finished, as shown at A, Fig. 1.
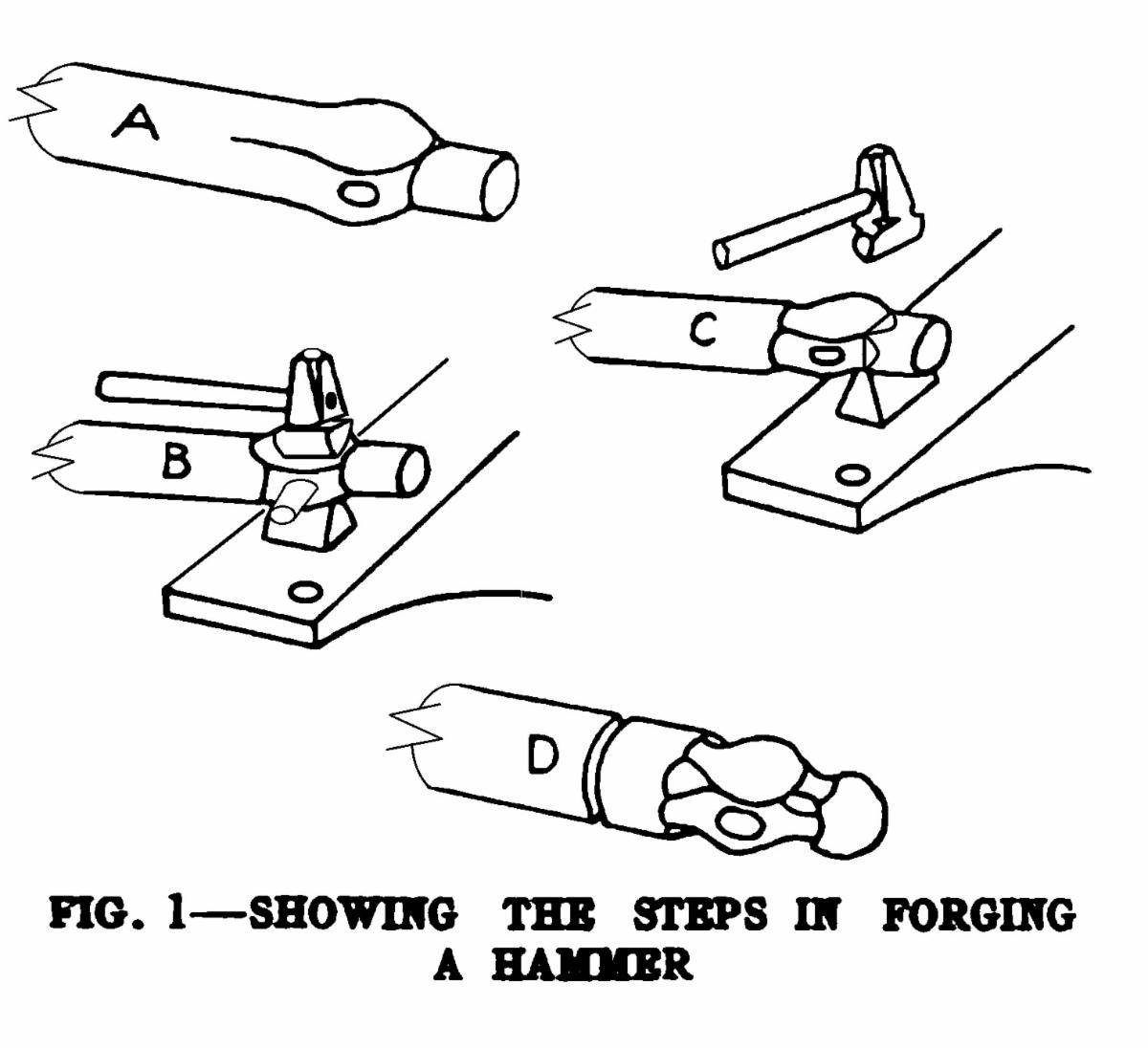 When the hole is punched one side of the eye will be a good deal thicker than the other. This is caused by the stock crowding in front of the punch as it is driven in. To overcome this the drift pin should be driven in from the thin side first and as much of the stock as possible worked back with fullers, as the eye is spread sideways, as shown at B. When the eye has been sufficiently spread on both sides and stands fairly central the sides are then finished smooth with a set hammer and a flatter. The drift pin should be oval shaped and taper, so that the eye will be wider at each end than it is in the center. This helps to keep a hammer firm upon the handle when it is properly wedged. The necks of a hammer each side of the eye are usually octagonal and are fullered to shape, as at C. When this has been done its appearance will be as shown at D. The face and pene can be finished to suit the ideas of the man who is to use it.
Hand-forged hammers are a great deal neater if a little filing is done to true up the octagon necks and to give the edges and sides of the eye a uniform and finished appearance, but polishing is unnecessary as hammers are generally used for work that defaces a fine finish. The face and pene, however, should be fairly smooth and true, so that there would be no danger of marking the work upon which they are used.
|
To harden and temper a hammer properly is a subject that has been frequently discussed and there still seems to be a good deal of difference in opinions. But the writer will give the method he has followed with success for over twenty years. Heat the pene to a bright cherry, keeping the heat as short as possible by packing fine green coal, that has been well watered, immediately behind the part that is being heated. When the proper temperature has been reached dip in a bath of cold water, where it should be kept until it is sufficiently cooled to carry water on the end. Now polish and draw temper with back heat until the color in approaching purple, when it should be cooled off or dipped long enough in water to prevent the temper running any lower. When this has been done heat the face in the same manner and as near as possible to the same temperature as the pene was heated, and cool off in a stream rising straight from the bottom of the quenching tub, as shown 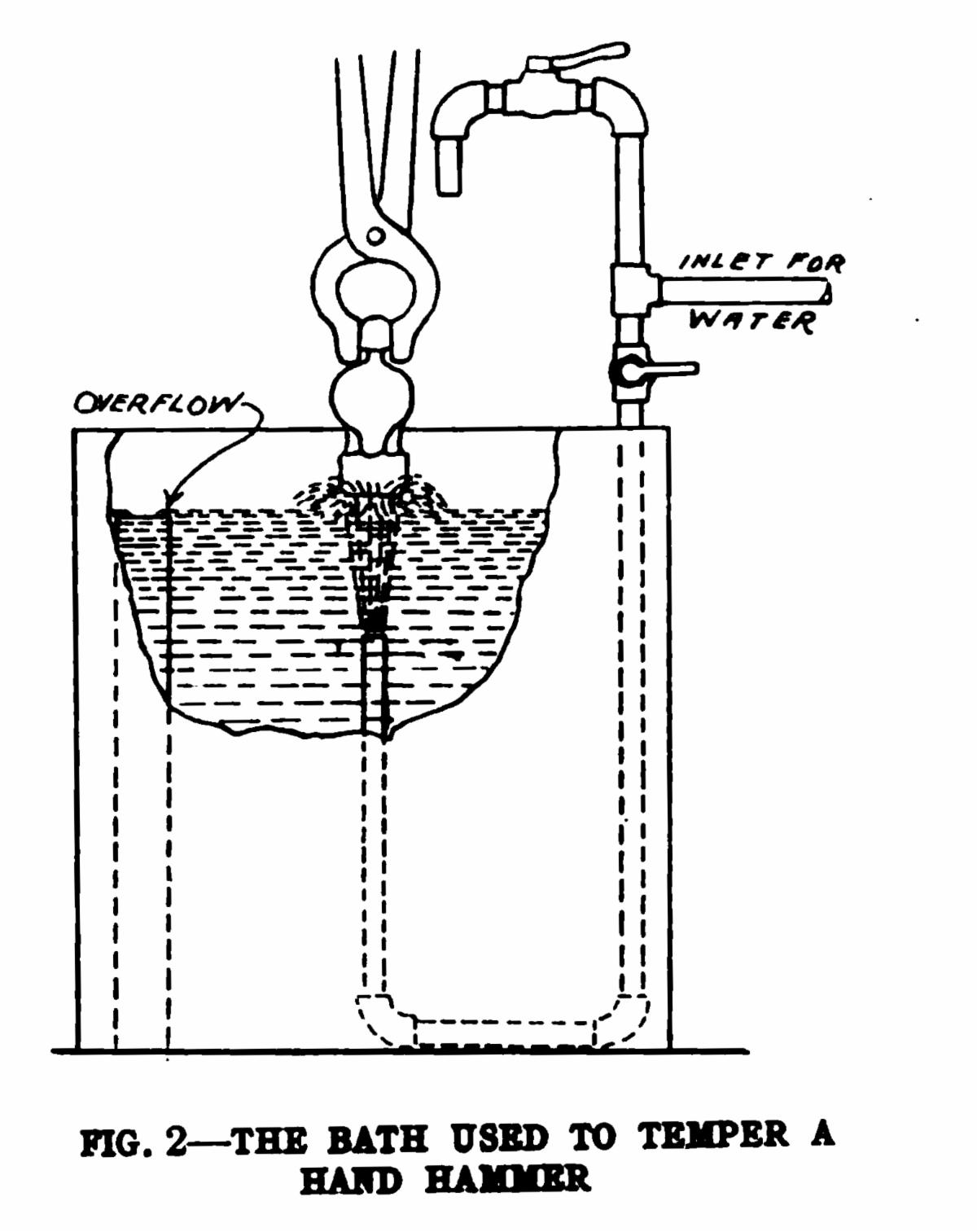 in Fig.2.
The stream should have just enough pressure to raise the water immediately over it about one inch above the level of the surrounding water. This prevents a cushion of steam forming on the center of the face and insures the center being as hard if not harder than the edges. When the face is fairly cooled remove from water, polish and draw the temper by placing in a hot fire just long enough to draw the edges to a dark blue, leaving the center as hard as possible. This gives a face that will neither chip nor batter down. The writer has a hammer that was made and hardened, as here described, over ten years ago.
|
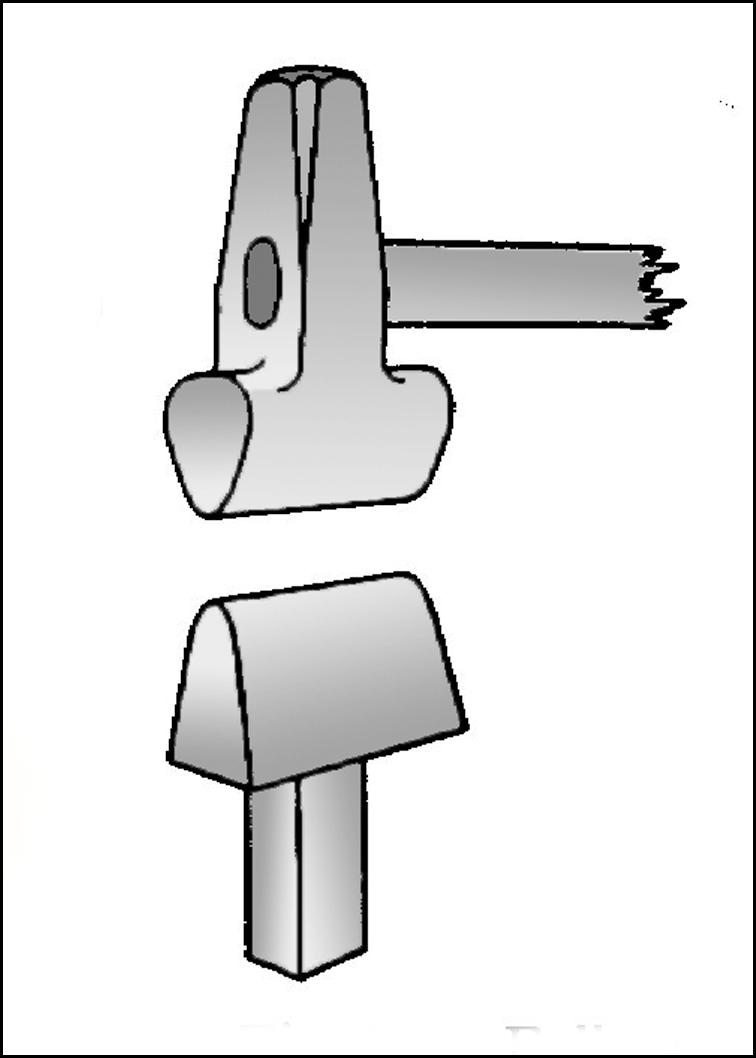 Forging Practice Carl G. Johnson American Technical Society Publishers Chicago, U.S.A. 1941 "Fullers, which are used for working grooves or hollows into shape, are also made top and bottom, as shown in [the illustration]. The top fuller is for finishing into round corners, around bosses, and on the inside of angles. The fuller is also used to spread metal when it is wished to work the metal only in one direction. The metal spreads at right angles to the working edge of the fuller." (p. 45)
|
|
|
|
Vernon J Mesler, Copyright © 2021. All Rights Reserved.
|
|
|
|