|
DAVID J. MARKS DESIGNER/CRAFTSMAN Newsletter July 2016
 |
|
|
|
Message From A Woodworker's Wife
Sensei: View top of vessel with threaded lid
"Perseverance":
Steadfastness in doing something despite difficulty or delay in achieving success.
indefatigability,
steadfastness purposefulness;
I am unabashedly saluting my husband for his perseverance in completing his newest creation Sensei.
As you have been reading in our newsletters for the last several months, David has been working day and nite on completing his vessel in time for the 2016 AAW Symposium in Atlanta, GA held on June 10 - 12. This was the 30th anniversary of the AAW Symposium and as usual drew an impressive international roster of demonstrators and attendees.
Drum roll please......yes, he finished it!!! He was literally applying Renaissance wax to the vessel the night before we took Sensei with us on the plane. He had finished the bentwood lamination stand in time to have that shipped out via Fed Ex, but with the vessel David was down to the wire.
The fact that there were new techniques that David learned so he could apply them to the vessel, that after moving mountains teaching nonstop he carved out windows of time to work on the piece, and he never, ever, gave up, really inspires me. Yes, there were definitely many nites when dinner did not happen until 10:30 pm, and he was basically in a rhythm of work, eat, sleep, work, eat, sleep. I do not recommend that as an ongoing lifestyle, but once in a while stepping up to the challenge and being willing to make the sacrifices to pursue your dream, is really, really worth it.
No matter what happens now, Sensei is completed and fully actualizes the vision David had in his head. He wanted to make something big, something he had never tried before, and absolutely did not back down if certain processes at first seemed too insurmountable. That can be hard to live with, but also awesome to behold once you see the final result.
|
In December of 2014 my friend Rik Lawrence, a furniture maker from nearby Sonoma (check out Red Cloud Furniture), called to offer to sell me a Big Leaf Maple tree which blew over in a storm on his property.
I saw this as an opportunity to get some large pieces of Maple for hollow vessel turning so I rented a truck with a hydraulic lift gate and called my friend Josh Caplan to help me with this big project.
I tried to mill some of the logs by hand with my chainsaw but soon realized that this was a job for a portable bandsaw mill, so I called my friend Shawn Gavin to get the job done.
Here is Shawn Gavin in his straw hat operating his portable wood mizer band saw mill.
The first log that I decided to turn weighed approximately 400 lbs which required my engine hoist to lift it into place.
After rough turning it, I needed to prevent it from cracking until I had the time in between teaching classes to get back to my lathe.
I decided to get some plastic drums and begin storing all of the milled logs underwater to prevent them from cracking.
I was able to work on the vessel in between my busy teaching schedule for a while.
The following year I was invited to do 4 demonstrations for the American Association of Woodturners 30th annual symposium in Atlanta Georgia in June of 2016 which gave me a specific goal and deadline to complete a large vessel and display it in front of a very large audience.
As everyone knows who does any type of woodworking, sometimes the project takes on a life of its own.
This was definitely the case with "Sensei".
Yes, I named this hollow vessel "Sensei" because it means teacher in Japanese and this vessel became my teacher and taught me a tremendous amount of new knowledge.
|
Scrapers DVD
15% Off Sale!!!!!!
A sharp card scraper is an excellent way to smooth and blend a curve and eliminate any ridges left by your gouges.
David's
Scrapers DVD gives you step by step instruction on how to sharpen a card scraper, as well as a gooseneck scraper which can be used on the inside of a bowl.
|
Student Feedback on Consult & Project Results
Topic for Consult: Working with Cocobolo to Make End Tables
David and Victoria,
I have completed the Cocobolo end tables and would like to thank you for your advice. I must have discussed this project and my troubles of finishing cocobolo with 8 people including woodworkers, wood suppliers and even manufacturers of finishes even one you had recommended I speak to.
I must say I gathered quite a lot of advice along the way. I will tell you however I found yours to be the most beneficial and I'll tell you why. You guided me to seek other woodworkers experiences and knowledge. Which I did and was able to use. You gave me the name of a product but told me to discuss my project with the developer of that product. You found my technique acceptable and said so. Others only told me what they would do.
It has been a while since your show was aired on tv but I remember your attention to details and approach was methodical.
With all of that on the table I discovered I needed to refine my technique and all the direction in the world will help but it won't put the finish on the wood. That was up to me. That I found in your advice.
Overall, it took three attempts to achieve my desired look. The last application went like this. I wiped the slabs with acetone, waited 10 minutes for that to dry (Steve Smith had thought I wasn't letting the acetone dry enough and it was getting trapped) and then I applied three coats of shellac. This time a 1lb cut. After a light sanding with 400 grit sand paper I applied 3 thin coats of Waterlox with light sanding between with an even finer grit.
When I had applied the Waterlox liberally (which was my second attempt) it took away the wood and looked and felt like it was coated in plastic. It was also not smooth and I was not satisfied with that finish.
When asked by a few fellow woodworkers if I'd ever work with cocobolo again. Thinking I'd say no, they were surprised when I said hell yeah this wood is amazing. And after all that I've learned along the way why waste that new knowledge.
Thank you again for your consultation and sharing your knowledge on WoodWorks. I was a huge fan. I hope you like the tables.
Sincerely,
Paul
David's Response:
Wow ! Paul, your Cocobolo tables look amazing !!
I'm very glad to hear that my consultation with you went well and that you were able to successfully finish these
magnificent
slabs of Cocobolo.
Cocobolo is a very challenging wood to finish due to the high levels of naturally occurring oils in this wood.
I know when I began finishing wood in the early 70's, I experienced much frustration due to the long learning curve.
We all reach a point when we ask ourselves if it's worth all of the headaches.
The truth is that the more we encounter problems in life, finishing or otherwise, and make a decision to forge
ahead and learn and solve these various problems, the stronger we become.
Thank you very much Paul for your compliments on my show Woodworks.
I congratulate you for pursuing answers to finishing this age old challenging wood.
It's extremely satisfying for me to be in a position to help my fellow woodworkers and to witness their success !
Thank you very much for sharing the photos of your beautifully finished cocobolo tables.
Cheers,
David
Need help with a project? David offers phone and email consultations:
Consult
|
2016 TEACHING SCHEDULE
Gilding & Chemical Patination: 2 Sessions Offered!
3 Days Hands On for Each Session
1) July 8 - 10,2016
**** JULY SESSION SOLD OUT*****
-OR -
2) December 2 - 4,2016
Class Size 5 - 10 Students Class Fee: $600.00 - All materials included. Skill Level: Beginning - Intermediate - Advanced
David has expanded this class to 3 days to provide more time to go over the gilding and patina processes. Even if you have taken this class previously, this newly expanded class will include the use of frisket and other techniques to expand your capabilities. The processes that you will learn can be applied to any surface that will accept paint. These include wood, metal, paper, ceramics, glass, even plastics. So no matter if you are a jeweler, ceramicist, sculptor, blacksmith, woodworker or woodturner, you will take home some very creative and innovative techniques to enhance your work and increase your marketability.
July 22 - 24, 2016 Marquetry & Inlay 3 Days Hands On
|
Student project in progress 2014 Marquetry & Inlay Class
|
|
Student project from previous Marquetry & Inlay class
|
Class Size: 3 - 10 students Class Fee $775.00 - All materials included. Skill Level: Beginning - Intermediate
In this hands-on class David will teach the challenging and artistic world of marquetry. He will explore several different methods of creating one of a kind inlays that will enhance your work and take it to the next level. David will show you how to do free hand inlay, router template inlay, double bevel marquetry (which is a veneering technique as opposed to an inlay technique), and colored epoxy inlay. He will show students how to do repeatable inlays by teaching you how to design and make your own templates.
October 6 - 10, 2016 Creative Bowl Turning 5 Days Hands On
|
2015 Creative Bowl Turning Clas
|
Sold Out! Use the CONTACT US Form to be put on the Wait List
Class Size: 3 - 10 students Class Fee: $875.00 - All materials included. Skill Level: Beginning to Intermediate All Skill Levels Welcome.
In this class students will get to experiment with different woods and different shapes to create their own individual designs. Students will turn bowls and small hollow vessels and decorate them with segmented rings made of ebony and other exotic woods. Students can also add gilding and chemical patination to embellish their bowls and vessels. David will teach sharpening techniques as well as design techniques.
November 10 - 13, 2016 Bentwood Lamination 4 Days Hands On
|
Ebony Stand for Alchemist Vessel is an example of bent lamination
|
Class Size: 3 - 10 students Class Fee: $875.00 - All materials included. Skill Level: Beginning to Intermediate
Bent lamination is one of woodworking's most exciting techniques. You can take any wood and slice it thin enough for it to bend. For example, David makes stands for his hollow vessels out of ebony and the legs are a tapered bentwood lamination utilizing 5 layers that are a 1/32 of an inch flaring to an 1/16 of an inch. By the time they are glued together, David has a curved leg that is 5/16 of an inch thick at the top, and a little over 1/8 inch thick at the foot.
In this class students will learn how to design & build their own bent lamination forms,
re-saw lumber, learn specific gluing techniques, and how to shape & use joinery for their completed laminations.
|
David Answers Your Questions
Subject: Gilding Project: Sealing the Piece for Protection
Hi David,
After reading an article that you wrote on the gilding process, I have a question about the sealing of the piece for protection. You wrote that you used Shellac or acrylic lacquer. Then when that dries you apply another coat of shellac or lacquer . Would there be a problem if I just used Satin Clear brushing Lacquer to seal and as a final coat?
Regards,
Steve
David's Answer:
Hi Steve,
You could try using satin clear brushing lacquer on a test sample board and see what happens.
I use Gloss Krylon acrylic lacquer for the first coat to preserve the colors. I always build my clear coats with gloss finishes for maximum clarity. For a satin finish, I will use a satin lacquer for my final one or two coats. Often times I'll use 0000 steel wool and hand rub the clear finish to a satin sheen.
The size (aka leaf adhesive, aka gilder's varnish) is oil based. Lacquer and oil based finishes are incompatible and there is a risk of the oil based varnish reacting with the lacquer in the form of cracking, bubbling, and crazing.
Dewaxed Shellac is compatible with just about all finishes although sometimes it reacts with the patina on Silver and causes the blues to turn a golden color which I don't want.
My solution to this problem is to use the best qualities of each finish. I spray a light coat of acrylic lacquer (acrylic lacquer will remain clear, nitrocellulose lacquer will turn amber over the years) first to seal in the colors.
I allow that to dry overnight at 70 to 75 degrees.
The next day I spray a light coat of dewaxed shellac and allow that to dry overnight at 70 to 75 degrees.
At this point the project is sealed and any finish will be compatible over the cured shellac.
I have been using Sherwin Williams CAB acrylic lacquer because nitrocellulose lacquer will turn an amber/yellow color over time and I want my sliver leaf to remain silver, also it is a durable finish
When I teach classes, I constantly remind my students to make lots of test sample boards and write down on the back of the board all of the steps that you have completed in as much detail as possible including the date and the temperature.
Keeping the finishes warm, in the 70 to 75 degree range is very important and the clear finishes will cure well with good clarity if you follow this rule.
I do offer
Consultations via email or phone if you need more in-depth information.
I charge $37.50 for 15 minutes.
I hope you find this information helpful. All the best to you in your artwork.
David
|
Phone Consults Available
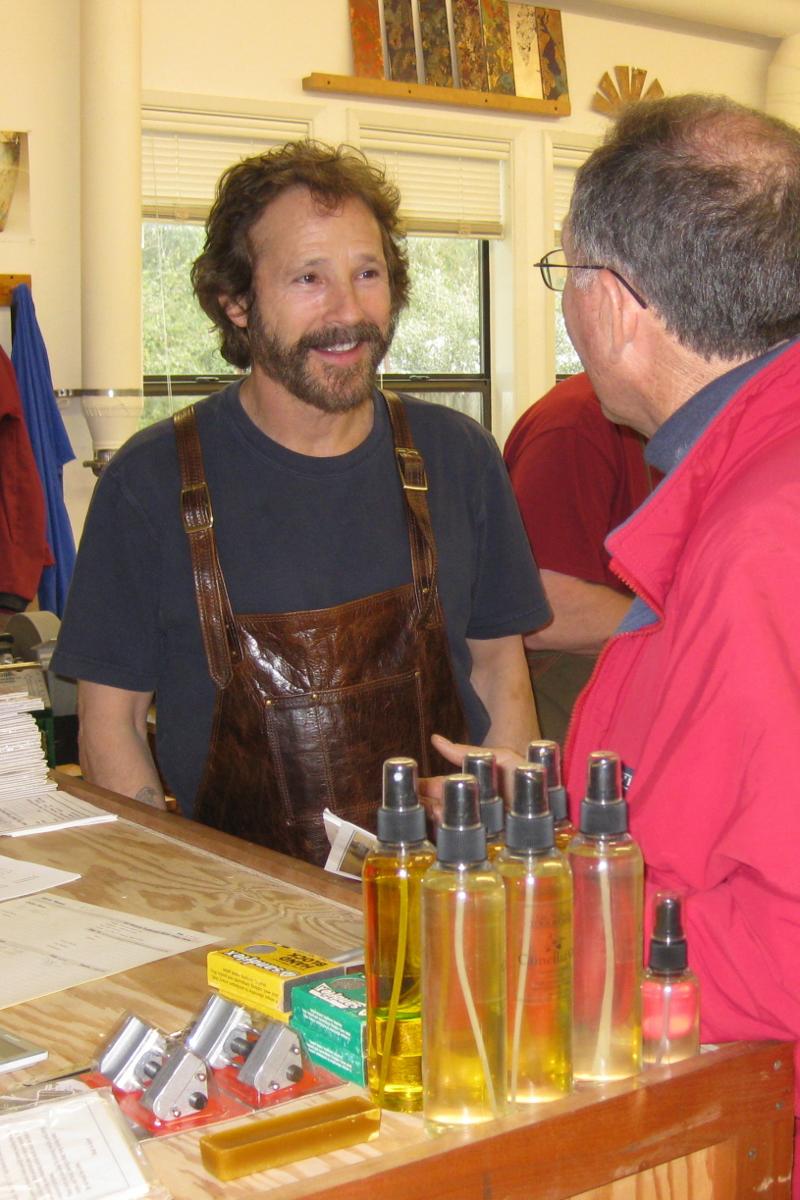
Are you working on a project and have hit an impasse? Can't find the answer you are looking for in any book, magazine, DVD, or Online Forum? David has been a full time woodworker since 1972, which has given him a wealth of experience in problem solving to offer woodworkers with those challenging projects. You can email David your project question and then schedule a phone consult to go over David's recommendations.
$37.50 per 15 minutes please email david@djmarks.com
Here is feedback from a client who David recently consulted with on a project:
"Thanks so much for the consultation. You gave me tons of information I needed. I feel more confident now about starting the project."
|
Have You Seen Our Online Store?
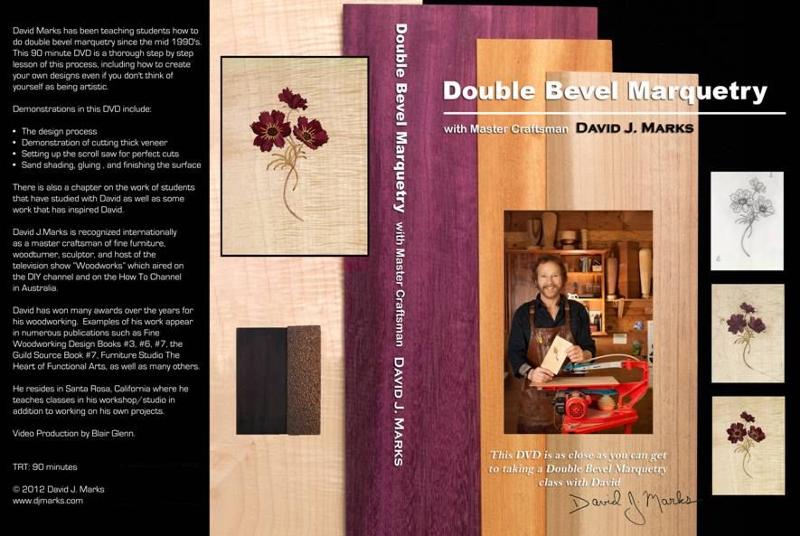 |
Double Bevel Marquetry DVD
|
David has a variety of woodworking and woodturning products to inspire, to educate, and to help with your projects. He has woodworking plans from many of the projects he created on his television show Woodworks, plus educational DVDs, Easy Wood Tools products, Metal Leaf & Patination Kit for gilding & chemical patination, and more.
Store
|
INFORMATION: David J Marks Designer Craftsman 2128 Marsh Road Santa Rosa, California 95403 LINKS: David J. Marks Website Store Classes Schedule Classes Photos Contact Sculptures Studio Furniture |
|
|
|
|
|